Process for producing organic semiconductor element, organic semiconductor element, and organic semiconductor device
A technology for organic semiconductors and manufacturing methods, which is applied in the fields of semiconductor/solid-state device manufacturing, semiconductor devices, electrical components, etc., can solve the problems of deterioration of the active layer, difficulty in fine and good pattern shape, etc., and achieves a minimal reduction effect.
- Summary
- Abstract
- Description
- Claims
- Application Information
AI Technical Summary
Problems solved by technology
Method used
Image
Examples
Embodiment 1
[0174] (manufacturing of transistors)
[0175] Next, a transistor is manufactured based on the transistor manufacturing method of the third embodiment described above. Figure 21 , 22 23 and 23 are diagrams showing the manufacturing process of the transistor of the first embodiment. First, if Figure 21 As shown in (a), a highly doped n-type silicon substrate 1 serving as a gate electrode and a substrate is prepared, and its surface is thermally oxidized to form a 200nm silicon oxide film to be an insulating layer 3 . Next, if Figure 21 As shown in (b), a 50nm-thick gold was evaporated on the surface of one insulating layer 3 of the substrate 1 by a vacuum evaporation method to form a source electrode 4a and a drain electrode 4b having lead lines and pads. The electrode at this time had a channel width of 500 μm and a channel length of 40 μm.
[0176] Next, according to the method described in the literature (S.R.Wasserman, et al., Langmuir, Vol.5, p1074, 1989), by immer...
Embodiment 2
[0185] (manufacturing of transistors)
[0186] In Example 2, a transistor including an active layer including poly(3-dodecylthiophene) was produced by performing the same steps as in Example 1 except for the following changes. That is, the points changed from Example 1 are: (a) the channel length is 200 μm instead of 40 μm; processing; (c) as a material for forming the semiconductor film 8, a chloroform solution of poly(3-dodecylthiophene) was used instead of a chlorobenzene solution of poly(3-hexylthiophene); (d) the support film 7 was replaced by A poly(1-methylpentene) film is replaced by a polyethylene film that has not been subjected to oxygen plasma treatment; (e) the condition of the stretching operation of the laminate 5 is replaced by 4 times of uniaxial stretching at 175° C., Uniaxially stretched 5 times at 100°C; (f) when forming the mask layer 156, the drying of the solution of polyvinyl alcohol was replaced by heat treatment at 80°C for 1 hour, and at 70°C for 1 ...
PUM
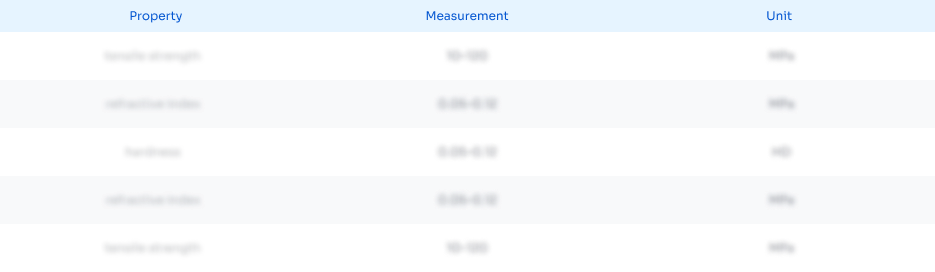
Abstract
Description
Claims
Application Information

- R&D
- Intellectual Property
- Life Sciences
- Materials
- Tech Scout
- Unparalleled Data Quality
- Higher Quality Content
- 60% Fewer Hallucinations
Browse by: Latest US Patents, China's latest patents, Technical Efficacy Thesaurus, Application Domain, Technology Topic, Popular Technical Reports.
© 2025 PatSnap. All rights reserved.Legal|Privacy policy|Modern Slavery Act Transparency Statement|Sitemap|About US| Contact US: help@patsnap.com