Rotary decelerating and braking energy recovery system of hydraulic excavator
A technology for braking energy recovery and hydraulic excavators, which is applied to earth movers/shovels, construction, etc., can solve the problem of increased engine load changes of excavators, affecting the operating habits and work efficiency of operators, and reducing engine output. minor issues
- Summary
- Abstract
- Description
- Claims
- Application Information
AI Technical Summary
Problems solved by technology
Method used
Image
Examples
Embodiment Construction
[0019] as attached figure 1As shown, the outlet of the hydraulic pump 17 communicates with the oil inlet port of the multi-way valve 21, the first pilot oil port of the multi-way valve 21 communicates with the second outlet of the pilot oil circuit control handle 14, and the second pilot oil port of the multi-way valve 21 The oil port communicates with the first outlet of the pilot oil circuit control handle 14; the first oil outlet of the multi-way valve 21 communicates with the first inlet of the first hydraulic control reversing valve 9 and the outlet of the first one-way valve 7 respectively, The oil outlet of the first hydraulically controlled reversing valve 9 is connected with the inlet of the rotary motor 11, the second inlet of the first hydraulically controlled reversing valve 9 is connected with the inlet of the first hydraulically controlled reversing valve 5, the first hydraulically controlled unloading valve 3 The inlet of the second one-way valve 1 and the inlet...
PUM
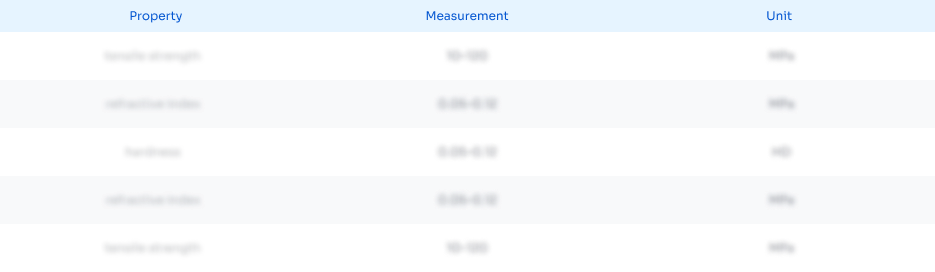
Abstract
Description
Claims
Application Information

- Generate Ideas
- Intellectual Property
- Life Sciences
- Materials
- Tech Scout
- Unparalleled Data Quality
- Higher Quality Content
- 60% Fewer Hallucinations
Browse by: Latest US Patents, China's latest patents, Technical Efficacy Thesaurus, Application Domain, Technology Topic, Popular Technical Reports.
© 2025 PatSnap. All rights reserved.Legal|Privacy policy|Modern Slavery Act Transparency Statement|Sitemap|About US| Contact US: help@patsnap.com