Hydraulic motor provided with friction pair with nanometer graphite layer and method for processing nanometer graphite layer
A nano-graphite, hydraulic motor technology, applied in the direction of liquid variable capacity machinery, reciprocating piston engine, variable capacity engine, etc., can solve the low speed performance and poor starting performance of the motor, the reliability and life problems are difficult to solve, and the hydraulic motor The problems of large volume and weight can improve the bearing capacity and mechanical efficiency, reduce the friction coefficient, and reduce the production cost.
- Summary
- Abstract
- Description
- Claims
- Application Information
AI Technical Summary
Problems solved by technology
Method used
Image
Examples
Embodiment 1
[0032] This embodiment is to process the nano-graphite layer on the outer surface of the plunger.
[0033] 1. Paint
[0034] Coat the parts of the plunger and the connecting rod that do not need to be plated with nano-graphite layer with epoxy resin paint and let it dry.
[0035] 2. Degreasing
[0036] Prepare by adding 22g of sodium hydroxide, 27g of sodium carbonate and 27g of trisodium phosphate per liter of water, and stir evenly to form a degreasing liquid. Heat the degreasing solution to 60°C, put the plunger into the degreasing solution, and soak for 15 minutes;
[0037] 3. Washing
[0038] Remove the plunger from the degreasing solution and rinse with running tap water.
[0039] 4. Activation
[0040] Prepare by adding 60g of zinc dihydrogen phosphate, 60g of zinc nitrate and 3g of sodium fluoride per liter of water, and stir evenly to form a derusting activation solution. The plunger after rinsing is soaked in the derusting activation solution under normal tempe...
Embodiment 2
[0047] In this embodiment, the nano-graphite layer is processed on the spherical surface of the ball head at one end of the connecting rod and the concave arc surface of the sliding shoe at the other end.
[0048] 1. Paint
[0049] Coat the surface of the part of the connecting rod that does not need to be plated with nano-graphite, and let it dry.
[0050] 2. Degreasing
[0051] Prepare by adding 25g of sodium hydroxide, 30g of sodium carbonate and 30g of trisodium phosphate per liter of water, and stir evenly to form a degreasing night. Heat the degreasing material to 65°C, put the connecting rod into the degreasing material and soak for 12 minutes;
[0052] 3. Washing
[0053] Take the connecting rod out of the degreasing room and rinse it with running tap water.
[0054] 4. Activation
[0055] Prepare by adding 75g of zinc dihydrogen phosphate, 80g of zinc nitrate and 4g of sodium fluoride per liter of water, and stir evenly to form a derusting activation solution. P...
Embodiment 3
[0062] In this embodiment, the nano-graphite layer is processed on the spherical surface of the ball head at one end of the connecting rod and the concave arc surface of the sliding shoe at the other end.
[0063] 1. Paint
[0064] Coat the surface of the part of the connecting rod that does not need to be plated with nano-graphite, and let it dry.
[0065] 2. Degreasing
[0066] Prepare by adding 28g of sodium hydroxide, 33g of sodium carbonate and 33g of trisodium phosphate per liter of water, and stir evenly to form a degreasing night. Heat the degreasing material to 70°C, put the connecting rod into the degreasing material and soak for 10 minutes;
[0067] 3. Washing
[0068] Take the connecting rod out of the degreasing room and rinse it with running tap water.
[0069] 4. Activation
[0070] According to the concentration of adding 90g zinc dihydrogen phosphate, 100g zinc nitrate and 6g sodium fluoride per liter of water to prepare, and stir evenly to form derusting...
PUM
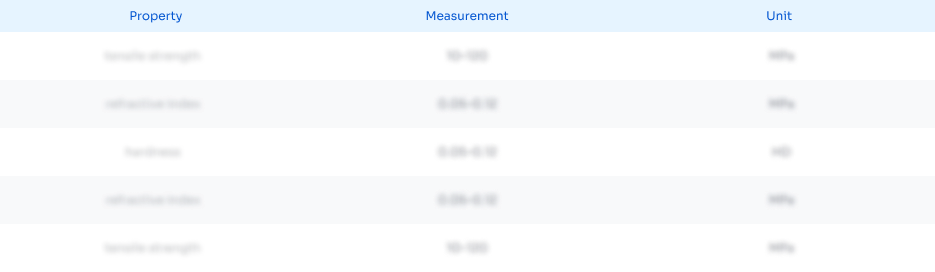
Abstract
Description
Claims
Application Information

- R&D Engineer
- R&D Manager
- IP Professional
- Industry Leading Data Capabilities
- Powerful AI technology
- Patent DNA Extraction
Browse by: Latest US Patents, China's latest patents, Technical Efficacy Thesaurus, Application Domain, Technology Topic, Popular Technical Reports.
© 2024 PatSnap. All rights reserved.Legal|Privacy policy|Modern Slavery Act Transparency Statement|Sitemap|About US| Contact US: help@patsnap.com