Production method by connecting two cement grinding machine in series
A production method, cement powder technology, applied in cement production, grain processing, etc., can solve the problems of high labor intensity, many production personnel, and low cement fineness surface, so as to reduce the energy consumption of electricity and coal, improve production efficiency, and save cost effect
- Summary
- Abstract
- Description
- Claims
- Application Information
AI Technical Summary
Problems solved by technology
Method used
Examples
Embodiment approach
[0007] According to the production of mechanical shaft kiln with more than 100,000 tons, the size of the mill is 2.2m-3.2m-4m, and the mill of one specification is operated in series, that is, the production method of two mills in series, and the compartment of the mill is changed. The location, the mill generally has two warehouses, and the space in the warehouse is divided into 33% and 40% of the original space. The second warehouse of the front mill is changed from the original one to a round steel ball crushing raw material for grinding, and the second mill in series The front warehouse was changed to a round rectangular steel forging.
PUM
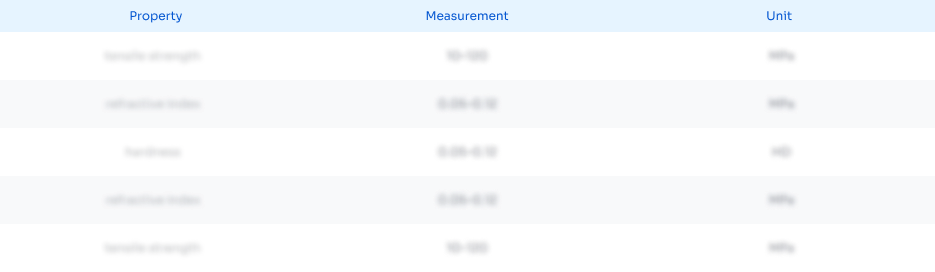
Abstract
Description
Claims
Application Information

- R&D Engineer
- R&D Manager
- IP Professional
- Industry Leading Data Capabilities
- Powerful AI technology
- Patent DNA Extraction
Browse by: Latest US Patents, China's latest patents, Technical Efficacy Thesaurus, Application Domain, Technology Topic, Popular Technical Reports.
© 2024 PatSnap. All rights reserved.Legal|Privacy policy|Modern Slavery Act Transparency Statement|Sitemap|About US| Contact US: help@patsnap.com