Polypropylene spinning oil agent and manufacturing method thereof
A polypropylene spinning and oiling technology, applied in textile and papermaking, fiber type, fiber processing and other directions, can solve the problems of environmental pollution, not easy to biodegrade, etc., and achieve good bundling, good stretching condition, uniform and stable oiling Effect
- Summary
- Abstract
- Description
- Claims
- Application Information
AI Technical Summary
Problems solved by technology
Method used
Image
Examples
Embodiment Construction
[0032] The specific process of making the polypropylene spinning finish of the present invention is described below:
[0033] 1. Preparation of raw materials
[0034] 1. Smoothing agent
[0035] The smoothing agent is one or a mixture of mineral oil, dihydric alcohol ester, trihydric alcohol ester, tetrahydric alcohol ester and fatty acid polyethylene glycol ester. The following table is the specific weight percentage of each composition in the smoothing agent:
[0036] Example
Diol ester
C 6 -C 20 trimethylol ester
C 12 -C 18 pentaerythritol ester
1
Mineral oil (5#) 24%
Fatty acid (C12-18) polyethylene
Glycol Esters 18%
trimethylolpropane oleate
58%
2
Mineral oil (20#) 33%
Oleic Acid Polyethylene Glycol (400) Mono
Ester 40%
Pentaerythritol Oleate 27%
3
Fatty acid (C12-18) polyethylene
Glycol ester ...
PUM
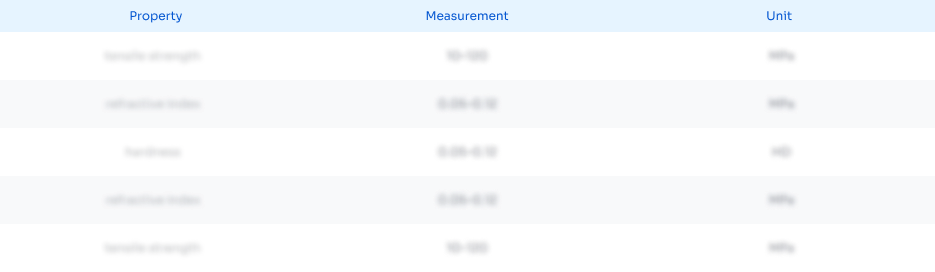
Abstract
Description
Claims
Application Information

- R&D
- Intellectual Property
- Life Sciences
- Materials
- Tech Scout
- Unparalleled Data Quality
- Higher Quality Content
- 60% Fewer Hallucinations
Browse by: Latest US Patents, China's latest patents, Technical Efficacy Thesaurus, Application Domain, Technology Topic, Popular Technical Reports.
© 2025 PatSnap. All rights reserved.Legal|Privacy policy|Modern Slavery Act Transparency Statement|Sitemap|About US| Contact US: help@patsnap.com