Method for machining high-precision sealing surface by numerical control gantry mill
A sealing surface, high-precision technology, applied in the direction of metal processing equipment, milling machine equipment, manufacturing tools, etc., can solve the problems that affect the processing quality and the effect of red and blue oil inspection, the flatness cannot meet the standard requirements, and the product appearance quality is poor. , to reduce the risk of scrapping, save time, and eliminate the effect of cutting tool marks
- Summary
- Abstract
- Description
- Claims
- Application Information
AI Technical Summary
Problems solved by technology
Method used
Image
Examples
Embodiment Construction
[0029] like image 3 , Figure 4 and Figure 5 As shown, for a certain type of combustion chamber shell, the length × width of the sealing surface is: 3250mm × 1320mm. The key area requires 100% contact of red and blue oil inspection. The plane is processed by the usual method, which cannot meet the requirements and needs to be reworked many times. The average The working hours of dragon milling for repairing each set are ~8-10 hours / set, and the working hours for fitter training are ~160 hours / set. After inspection, it is found that the Z-axis movement direction of the gantry milling machine is not perpendicular to the X-axis direction, that is, the tool plane 4 and the ideal plane 5 have an error angle α°, so that when the processing is viewed on the z-x plane, there will be tool marks on the machining plane 6, Viewing the machining on the y-z plane, there will be tool marks and concaves on the machining plane 6.
[0030] Weld the process lap on the appropriate part of th...
PUM
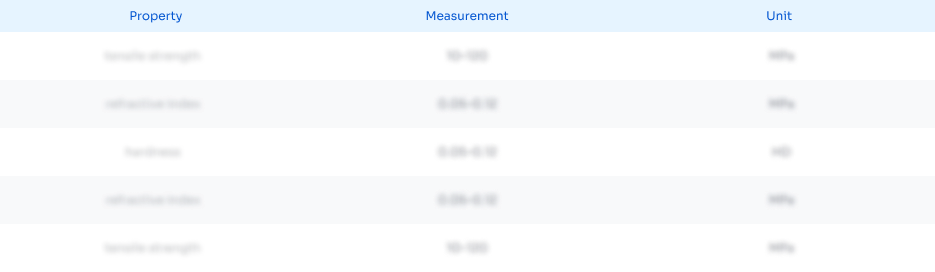
Abstract
Description
Claims
Application Information

- Generate Ideas
- Intellectual Property
- Life Sciences
- Materials
- Tech Scout
- Unparalleled Data Quality
- Higher Quality Content
- 60% Fewer Hallucinations
Browse by: Latest US Patents, China's latest patents, Technical Efficacy Thesaurus, Application Domain, Technology Topic, Popular Technical Reports.
© 2025 PatSnap. All rights reserved.Legal|Privacy policy|Modern Slavery Act Transparency Statement|Sitemap|About US| Contact US: help@patsnap.com