4-Method for synthesizing 4-Methyloctanoic Acid
A technology of methyl octanoic acid and a synthesis method, which is applied in the preparation of carboxylate/lactone, organic chemistry, etc., can solve the problems of high preparation cost, high difficulty, rare raw materials, etc., and achieves reduced difficulty, mild reaction conditions, and high yield. rate effect
- Summary
- Abstract
- Description
- Claims
- Application Information
AI Technical Summary
Problems solved by technology
Method used
Image
Examples
Embodiment 1
[0015] Embodiment 1: the synthesis of 4-methyl-butylactone
[0016] In a 2L flask equipped with a mechanical stirrer, a thermometer, an addition funnel and a reflux condenser, add 48g (2mol) of magnesium shavings, 150mL of diethyl ether and a grain of iodine. Start stirring, add dropwise a mixture of 274g bromobutane (2mol) and 300mL diethyl ether, keep the reaction slightly boiling, complete the addition in about 2 hours, and then keep the temperature at 40°C for 1 hour. Cool the reaction liquid to -5°C, add dropwise a mixture of 260g methyl levulinate (2mol) and 150mL diethyl ether, and control the reaction temperature below 0°C. After the addition, stir at room temperature for 2 hours, carefully add 416g of saturated ammonium chloride aqueous solution to decompose, control the temperature at 10°C, and generate granular solid and almost dry ether layer. Pour off the ether layer, extract the solid with 2*250mL ether, distill the crude product under reduced pressure after dee...
Embodiment 2
[0017] Embodiment 2: the synthesis of 4-methyl-butylactone
[0018] In a 1L flask equipped with a mechanical stirrer, a thermometer, an addition funnel and a reflux condenser, add 24 g (1 mol) of magnesium shavings, 75 mL of diethyl ether and a grain of iodine. Start stirring, add dropwise a mixture of 140 g of bromobutane (1 mol) and 150 mL of diethyl ether, keep the reaction slightly boiling, complete the addition in about 2 hours, and then keep the temperature at 40°C for 1 hour. Cool the reaction liquid to -15°C, add dropwise a mixture of 156g methyl levulinate (1.2mol) and 150mL diethyl ether, and control the reaction temperature below -10°C. After the addition, stir at room temperature for 2 hours, carefully add 208 g of saturated ammonium chloride aqueous solution to decompose, control the temperature at 10 ° C, and generate granular solid and almost dry ether layer. Pour off the ether layer, extract the solid with 2*125mL ether, distill the crude product under reduced...
Embodiment 3
[0019] Embodiment 3: the synthesis of 4-methyl-butylactone
[0020] In a 2L flask equipped with a mechanical stirrer, a thermometer, an addition funnel and a reflux condenser, add 24 g (1 mol) of magnesium alloy, 100 mL of tetrahydrofuran, benzene (tetrahydrofuran:benzene=1:1) and a grain of iodine. Start stirring, add dropwise a mixture of 140g of bromobutane (1mol) and 200mL of tetrahydrofuran and benzene, keep the reaction temperature at about 45°C, complete the addition in about 2 hours, and then keep the temperature at 45°C for 1 hour. Cool the reaction liquid to -10°C, add dropwise a mixture of 156g of methyl levulinate (1.2mol) and 150mL of tetrahydrofuran and benzene, and control the reaction temperature below -5°C. After the addition, stir at room temperature for 2 hours, carefully add 350g of 10% hydrochloric acid to decompose, control the temperature at 10°C, wash the base layer with water until neutral, remove the solvent and distill the crude product under reduced...
PUM
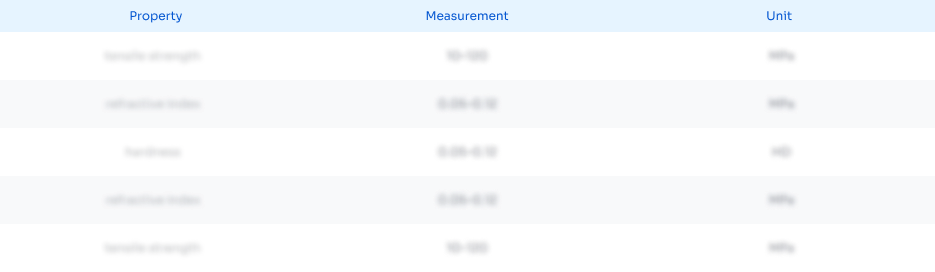
Abstract
Description
Claims
Application Information

- Generate Ideas
- Intellectual Property
- Life Sciences
- Materials
- Tech Scout
- Unparalleled Data Quality
- Higher Quality Content
- 60% Fewer Hallucinations
Browse by: Latest US Patents, China's latest patents, Technical Efficacy Thesaurus, Application Domain, Technology Topic, Popular Technical Reports.
© 2025 PatSnap. All rights reserved.Legal|Privacy policy|Modern Slavery Act Transparency Statement|Sitemap|About US| Contact US: help@patsnap.com