Method for mixing, rubbing and welding technique of 2A70 aluminium alloy cylindrical body (delta 20mm)
A technology of friction stir welding and process method, which is applied in the direction of metal processing equipment, manufacturing tools, welding equipment, etc., to achieve stable and reliable mechanical properties, improve the performance of welded joints, and have good use effects
- Summary
- Abstract
- Description
- Claims
- Application Information
AI Technical Summary
Problems solved by technology
Method used
Image
Examples
Embodiment Construction
[0019] See the specific welding process figure 1 Shown: Use the first stirring head to start welding from point A of the cylinder, stop welding after welding to point B, take the first stirring head out of the cylinder, and prepare the same material and heat treatment state as the cylinder , the keyhole pin with the same taper as the welding keyhole is plugged into the keyhole at point B, press the keyhole pin into the keyhole with the second stirring head, and then use the second stirring head to start from the first stirring head Restart welding at the welding keyhole, that is, start welding from point B. After completing the welding of the remaining welds of the cylinder to point A, take out the stirring head, and leave a welding keyhole at point A. After the welding is completed, X-ray and ultrasonic testing of the joints of the two stirring heads have found no defects, and the mechanical properties of the joints have been tested. The weld strength can reach more than 90% ...
PUM
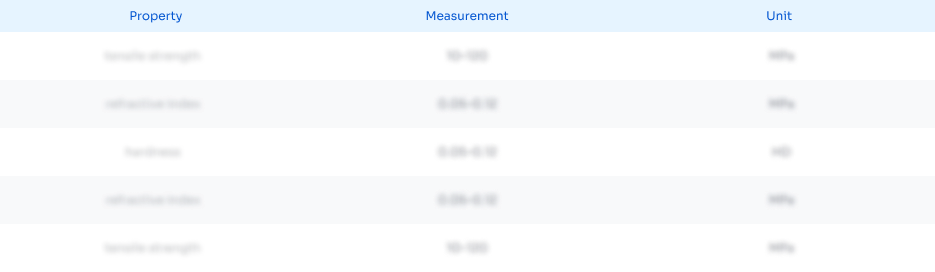
Abstract
Description
Claims
Application Information

- Generate Ideas
- Intellectual Property
- Life Sciences
- Materials
- Tech Scout
- Unparalleled Data Quality
- Higher Quality Content
- 60% Fewer Hallucinations
Browse by: Latest US Patents, China's latest patents, Technical Efficacy Thesaurus, Application Domain, Technology Topic, Popular Technical Reports.
© 2025 PatSnap. All rights reserved.Legal|Privacy policy|Modern Slavery Act Transparency Statement|Sitemap|About US| Contact US: help@patsnap.com