Heap-leaching method for separating copper and tin from tin-plated copper wires
A technology of tinned copper wire and heap leaching method, applied in the direction of improving process efficiency, can solve the problems of difficult mass production, expensive copper sulfate, difficult mass production, etc., to simplify the waste liquid treatment process and process Simple and easy to implement, reducing the effect of waste liquid removal
- Summary
- Abstract
- Description
- Claims
- Application Information
AI Technical Summary
Problems solved by technology
Method used
Image
Examples
Embodiment 1
[0020] Wash 10 kg of tin-plated copper wires with their skins removed, and stack them on an acid-proof and alkali-proof heap leaching table for heap leaching. The heap leaching solution is 100 kg, the concentration of copper sulfate in the heap leaching solution is 150g / L, and the concentration of sulfuric acid is 120mL , the heap leaching adopts the spray liquid distribution method, in which the temperature of the heap leaching liquid is 60°C, and the spraying intensity is 15L / (h·m 2 ), the heap leaching time is 4 hours; after the heap leaching, the heap leaching slag is pickled with the regenerated heap leaching liquid, and the solution after pickling is returned to the heap leaching process for the next heap leaching, and the heap leaching slag is washed with water to obtain detinned Copper wire, water washing solution is recycled; add hydrogen peroxide to the heap leaching solution until no white precipitate is produced, heat the above reaction solution to boil, then stop h...
Embodiment 2
[0022] Wash 10 kilograms of tinned copper wires with peeled wires in water, and pile them up on the anti-acid and anti-alkali heap leaching platform for heap leaching. The concentration of copper sulfate in the medium is 100g / L, the concentration of sulfuric acid is 250mL, and the heap leaching adopts the spray liquid distribution method, in which the temperature of the heap leaching solution is 55°C, and the spray intensity is 10L / (h·m 2 ), the heap leaching time is 2 hours; after the heap leaching, the heap leaching slag is pickled with the regenerated heap leaching liquid in Implementation Case 1, and the pickling solution is returned to the next heap leaching process for heap leaching. Wash with water to obtain detinned copper wire, and the washing solution is recycled; add hydrogen peroxide to the heap leaching solution until no white precipitate is produced, heat the above reaction solution to boil, then stop heating, and filter after standing for 24 hours; the filter res...
Embodiment 3
[0024] Wash 10 kilograms of tinned copper wires with peeled wires in water, and pile them up on an acid-proof and alkali-proof heap leaching platform for heap leaching. The concentration of copper sulfate in the medium is 75g / L, the concentration of sulfuric acid is 150mL, and the heap leaching adopts the spray liquid distribution method, in which the temperature of the heap leaching solution is 50°C, and the spray intensity is 20L / (h·m 2 ), the heap leaching time is 4 hours; after the heap leaching, the heap leaching slag is pickled with the regenerated heap leaching liquid in Implementation Case 2, and the pickling solution is returned to the next heap leaching process for heap leaching. After the pickling, the heap leaching slag is The detinned copper wire is obtained by washing with water, and the washing solution is recycled; hydrogen peroxide is added to the heap leaching solution until no white precipitate is produced, the above reaction solution is heated and boiled, th...
PUM
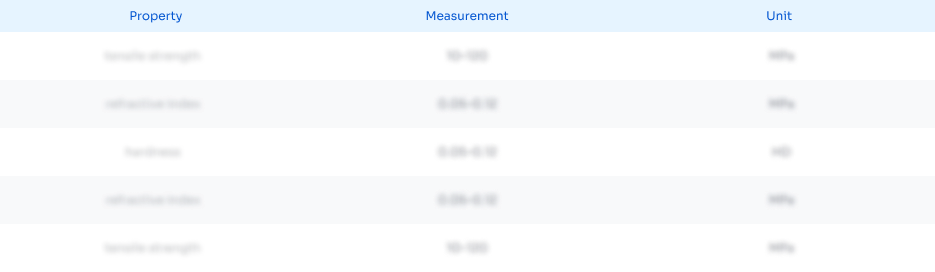
Abstract
Description
Claims
Application Information

- R&D Engineer
- R&D Manager
- IP Professional
- Industry Leading Data Capabilities
- Powerful AI technology
- Patent DNA Extraction
Browse by: Latest US Patents, China's latest patents, Technical Efficacy Thesaurus, Application Domain, Technology Topic, Popular Technical Reports.
© 2024 PatSnap. All rights reserved.Legal|Privacy policy|Modern Slavery Act Transparency Statement|Sitemap|About US| Contact US: help@patsnap.com