Method and device for preparing metal powder
A metal powder and metal liquid technology, which is applied in the field of powder metallurgy, can solve the problems that the mass density of the spray mist cannot be kept uniform, the diameter of the spray droplets is large, and the complexity of the equipment increases. It is easy to implement, with few intermediate transition mechanisms, The effect of easy implementation
- Summary
- Abstract
- Description
- Claims
- Application Information
AI Technical Summary
Problems solved by technology
Method used
Image
Examples
Embodiment 1
[0032] After heating the molten steel to 1650°C, tap the steel and pour it into the ladle. The flow rate of the molten steel is 1m / s. When it is filled to a height of 500mm, turn on the high-temperature drum, adjust the speed to 100rad / min, open the gas cooling nozzle, set the internal pressure to 0.8Mpa, and heat the bottom refractory material with the bottom heater to keep the temperature at 1350°C. After all the molten steel is sprayed, the powder is collected.
Embodiment 2
[0034] After heating the molten steel to 1630°C, tap the steel and pour it into the ladle. The flow rate of the molten steel is 1.2m / s. When the liquid is filled to a height of 600mm, turn on the high-temperature drum, adjust the speed to 120rad / min, open the gas cooling nozzle, set the internal pressure to 0.9Mpa, and heat the bottom refractory material with the bottom heater to keep the temperature at 1360°C. After all the molten steel is sprayed, the powder is collected.
Embodiment 3
[0036] After heating the molten steel to 1670°C, tap the steel and pour it into the ladle. The flow rate of the molten steel is 1.5m / s. When the liquid is filled to a height of 400mm, turn on the high-temperature drum, adjust the speed to 150rad / min, open the gas cooling nozzle, set the internal pressure to 1Mpa, and heat the bottom refractory material with the bottom heater to keep the temperature at 1300°C. After all the molten steel is sprayed, the powder is collected.
[0037] At present, most of the existing powder preparation processes are completed at the cost of consuming a large amount of inert gas, while the powder preparation process of the present invention uses mechanical energy to atomize molten steel, and the molten steel is pulverized by centrifugal force. During the atomization process, the flying direction is fixed, which facilitates the collection of powder, saves a lot of energy and gas resources, and reduces the cost; at the same time, the powder preparati...
PUM
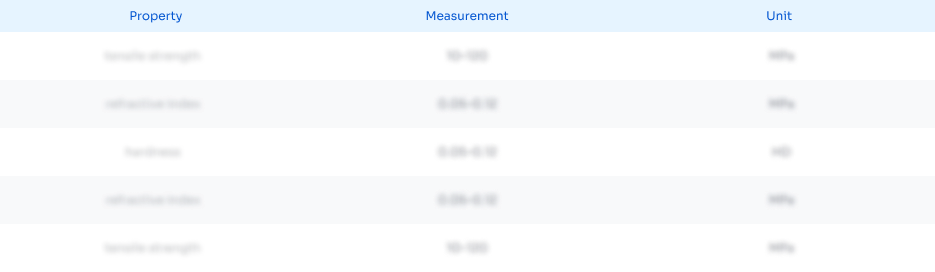
Abstract
Description
Claims
Application Information

- R&D Engineer
- R&D Manager
- IP Professional
- Industry Leading Data Capabilities
- Powerful AI technology
- Patent DNA Extraction
Browse by: Latest US Patents, China's latest patents, Technical Efficacy Thesaurus, Application Domain, Technology Topic, Popular Technical Reports.
© 2024 PatSnap. All rights reserved.Legal|Privacy policy|Modern Slavery Act Transparency Statement|Sitemap|About US| Contact US: help@patsnap.com