Sealing method for tube end of carbon steel/stainless steel composited tube
A stainless steel and composite pipe technology, applied in welding/welding/cutting items, welding equipment, welding media, etc., can solve the problem of high welding pass rate, achieve high welding pass rate, reduce the difficulty of sealing and welding, and reduce the effect of difficulty
- Summary
- Abstract
- Description
- Claims
- Application Information
AI Technical Summary
Problems solved by technology
Method used
Image
Examples
Embodiment 1
[0037] In this embodiment, the carbon steel / stainless steel composite pipe that is sealed and welded is a composite pipe composed of a stainless steel lining pipe 1 made of 316L stainless steel and a carbon steel base pipe 2 made of 20G carbon steel, and its specification is Φ76×(7+2)mm.
[0038] Step 1. Using conventional machining methods, remove a section of 10mm-long stainless steel lining pipe 1 from the outside to the inside at the end of the carbon steel / stainless steel composite pipe to be sealed and welded. In actual operation, a lathe is generally used to remove a section of 10mm-long stainless steel lining pipe 1 at the end of the carbon steel / stainless steel composite pipe to be sealed and welded.
[0039] Step 2: Process the inner side of the exposed carbon steel base pipe 2 after removing the stainless steel lining pipe 1 into an inwardly inclined slope from the outside to the inside, and the slope angle α of the slope is 5°, see figure 2 .
[0040] Step 3. Un...
Embodiment 2
[0044] In this embodiment, the carbon steel / stainless steel composite pipe that is sealed and welded is a composite pipe composed of a stainless steel lining pipe 1 made of 316L stainless steel and a carbon steel base pipe 2 made of 20G carbon steel, and its specification is Φ56×(5+1.5)mm. The difference from Example 1 is that in step one, a mechanical processing method is used to remove a section of stainless steel lining pipe 1 with a length of 8 mm from the outside to the inside at the end of the carbon steel / stainless steel composite pipe to be sealed and welded; in step two, by The inclination angle α of the inclined surface processed from the outside to the inside is 3°; the welding current during the surfacing welding in step 3 is 90A, and the flow rate of the shielding gas used in the welding process is 13L / min. After the surfacing welding is completed, a total of 3 layers of stainless steel surfacing welding layers 3 are formed on the inclined surface from inside to o...
Embodiment 3
[0047] In this embodiment, the carbon steel / stainless steel composite pipe that is sealed and welded is a composite pipe composed of a stainless steel lining pipe 1 made of 316L stainless steel and a carbon steel base pipe 2 made of 20G carbon steel, and its specification is Φ96×(9+3)mm. The difference from Example 1 is: in step one, a conventional mechanical processing method is used to remove a section of stainless steel liner pipe 1 with a length of 13 mm from the outside to the inside at the end of the carbon steel / stainless steel composite pipe; in step two, from the outside to the inside The inclination angle α of the bevel processed inside is 8°; the welding current during the surfacing welding in step 3 is 90A, and the flow rate of the shielding gas used in the welding process is 17L / min. After the surfacing welding is completed, a total of 5 layers of stainless steel surfacing welding layers 3 are formed on the inclined surface from inside to outside.
[0048] In thi...
PUM
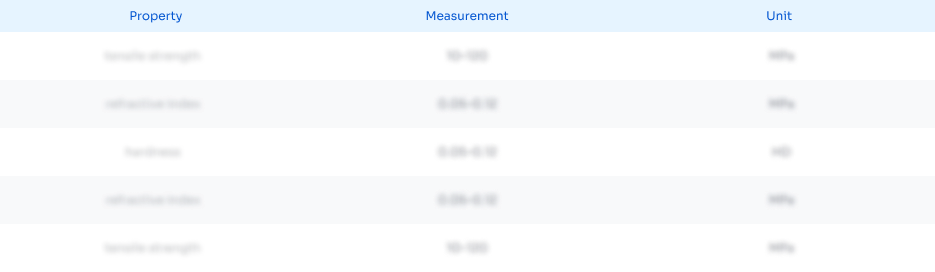
Abstract
Description
Claims
Application Information

- R&D Engineer
- R&D Manager
- IP Professional
- Industry Leading Data Capabilities
- Powerful AI technology
- Patent DNA Extraction
Browse by: Latest US Patents, China's latest patents, Technical Efficacy Thesaurus, Application Domain, Technology Topic.
© 2024 PatSnap. All rights reserved.Legal|Privacy policy|Modern Slavery Act Transparency Statement|Sitemap