Thickening agent synthesized by acrylic ester and preparation method thereof
A technology for synthesizing thickeners and acrylates, used in the field of acrylate synthesis thickeners and their preparation, can solve problems such as gaps and poor water holding capacity, and achieve good water holding capacity, strong electrolyte resistance, and high thickening ability. Effect
- Summary
- Abstract
- Description
- Claims
- Application Information
AI Technical Summary
Problems solved by technology
Method used
Image
Examples
preparation example Construction
[0051] The preparation method of functional monomer:
[0052] Add 400-800 parts of fatty amine polyoxyethylene ether into methyl methacrylate, mix well, add 0.5-5.0 parts of nitroxide free radical piperidinol, and 0.5-5.0 parts of sodium methoxide. After reacting at 75° C. for four hours, it was cooled for use.
[0053] The preparation of this acrylate synthetic thickener:
[0054]The formula is as follows:
[0055] 120-160 parts of acrylic acid;
[0056] 10-30 parts of acrylamide;
[0057] 150-300 parts of 25% ammonia water;
[0058] Functional monomer 10-30 parts;
[0059] 2-8 parts of EDTA;
[0060] 150-300 parts of deionized water;
[0061] 20-140 parts of odorless kerosene;
[0062] 3# white oil 20-140 parts;
[0063] 0.2-1.2 parts of dipropylene phthalate;
[0064] Ammonium persulfate 0.2-1.2 parts;
[0065] Span 80 5-20 copies;
[0066] 5-20 parts of isomerized cetyl alcohol polyoxyethylene ether.
[0067] The preparation method of acrylate synthetic thicke...
Embodiment 1
[0070] The first step, the synthesis of functional monomers:
[0071] Add 600 parts of aliphatic amine polyoxyethylene ether to 400 parts of methyl methacrylate, mix well, add 1.6 parts of nitroxide free radical piperidinol, 1.6 parts of sodium methoxide, and react at 75°C for four hours to prepare a functional monomer , cooled for later use.
[0072] The second step, the preparation of acrylate synthetic thickener:
[0073] Adopt the following formula:
[0074] Acrylic acid, 120 parts; acrylamide, 15 parts; 25% ammonia water, 150 parts; functional monomer, 10 parts; EDTA, 4 parts; deionized water, 200 parts; odorless kerosene, 90 parts; 3# white oil, 40 parts ; Dipropylene phthalate, 0.2 parts; Ammonium persulfate, 0.3 parts; Span 80, 6 parts; Isomerized cetyl alcohol polyoxyethylene ether, 6 parts.
[0075] Adopt following preparation method:
[0076] First vacuum the acrylamide dissolved in deionized water into the neutralization kettle, then vacuum the acrylic acid int...
Embodiment 2
[0078] The first step, the synthesis of functional monomers:
[0079] Add 400 parts of aliphatic amine polyoxyethylene ether to 400 parts of methyl methacrylate, mix well, add 1.6 parts of nitroxide free radical piperidinol, 1.2 parts of sodium methoxide, and react at 75° for four hours to prepare a functional monomer , cooled for later use.
[0080] The second step, the preparation of thickener:
[0081] Adopt the following formula:
[0082] Acrylic acid, 160 parts; acrylamide, 10 parts; 25% ammonia water, 200 parts; functional monomer, 10 parts; EDTA, 4 parts; deionized water, 150 parts; odorless kerosene, 70 parts; 3# white oil, 60 parts ; Dipropylene phthalate, 0.15 parts; Ammonium persulfate, 0.3 parts; Span 80, 6 parts; Isomerized cetyl alcohol polyoxyethylene ether, 6 parts.
[0083] Adopt following preparation method:
[0084] First vacuum the acrylamide dissolved in deionized water into the neutralization kettle, then vacuum the acrylic acid into the neutralizatio...
PUM
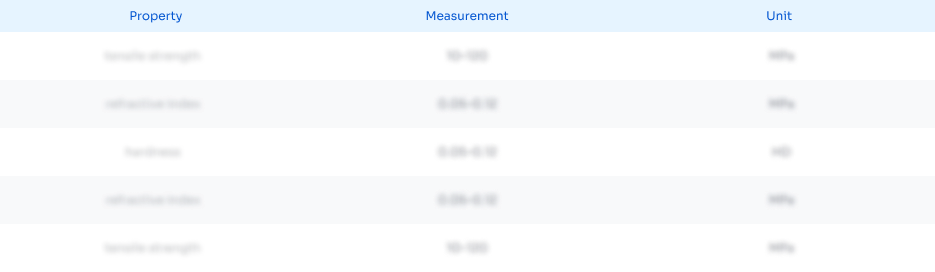
Abstract
Description
Claims
Application Information

- R&D Engineer
- R&D Manager
- IP Professional
- Industry Leading Data Capabilities
- Powerful AI technology
- Patent DNA Extraction
Browse by: Latest US Patents, China's latest patents, Technical Efficacy Thesaurus, Application Domain, Technology Topic, Popular Technical Reports.
© 2024 PatSnap. All rights reserved.Legal|Privacy policy|Modern Slavery Act Transparency Statement|Sitemap|About US| Contact US: help@patsnap.com