Low foamed multi-layer plastic building template and method for manufacturing same
A construction template and low-foaming technology, which is applied to the preparation of building components on site, construction, building construction, etc., can solve problems such as difficulties in recycling, poor quality of boards and adhesives, and difficulties in recycling, so as to benefit Human health, reduce construction costs, improve the effect of comprehensive performance
- Summary
- Abstract
- Description
- Claims
- Application Information
AI Technical Summary
Problems solved by technology
Method used
Image
Examples
example 1
[0022] Example 1: 60 parts of polyethylene, 35 parts of aluminum hydroxide, and 5 parts of liquid polyisobutylene are stirred and mixed, granulated by a granulator, and sent to 1# plastic extruder; 98 parts of polyethylene, azodicarboxylate 0.3 parts of barium oxide, 0.8 parts of zinc oxide, and 0.9 parts of liquid polyisobutylene are mixed and stirred and sent to 2# plastic extruder. The extruder mixture enters the surface layer, the 2# extruder mixture enters the core layer, and is continuously extruded to form a flat building formwork. The thickness of the surface layer 1 is 0.6mm, and the thickness of the core layer 2 is 13.8mm. After cooling, it is cut according to the specifications. ,like figure 1 .
example 2
[0023] Example 2: Send 78 parts of recycled polypropylene, 21 parts of zinc oxide, and 1 part of low molecular weight paraffin into 1# extruder, and feed 99.7 parts of recycled polypropylene, 0.1 part of azodicarbonamide, 0.1 part of barium oxide, and low molecular weight paraffin into 1# extruder. Measure 0.1 part of paraffin, send it into 2# extruder, the rest of the method is the same as Example 1, and make a flat template, the surface layer 1 is 1.0mm thick, and the core layer 2 is 16mm thick. Before complete cooling, it will be processed by forming a mold and controlling the appropriate temperature. Formwork at right angles, such as figure 2 .
example 3
[0024] Example 3: Send 87 parts of regenerated polyvinyl chloride, 10 parts of magnesium hydroxide, and 3 parts of animal fat into the 1# extruder, and feed 99 parts of regenerated polyvinyl chloride, 0.2 parts of p-toluenesulfonylchlorourea, and 0.3 parts of zinc oxide , 0.5 part of animal fat is sent into 2# extruder, and all the other methods are with example two, are processed into surface layer 1 thick 0.8mm, the groove template of core layer 2 thick 16.4mm, as image 3 .
PUM
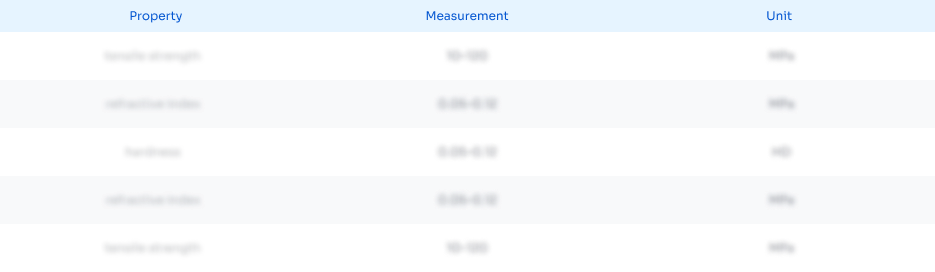
Abstract
Description
Claims
Application Information

- R&D
- Intellectual Property
- Life Sciences
- Materials
- Tech Scout
- Unparalleled Data Quality
- Higher Quality Content
- 60% Fewer Hallucinations
Browse by: Latest US Patents, China's latest patents, Technical Efficacy Thesaurus, Application Domain, Technology Topic, Popular Technical Reports.
© 2025 PatSnap. All rights reserved.Legal|Privacy policy|Modern Slavery Act Transparency Statement|Sitemap|About US| Contact US: help@patsnap.com