Molten metal oxidation-resistant chelating reducer
A technology of melting metal and oxidizing chelate, applied in the direction of metal material coating process, etc., can solve the problems of carcinogens, low reduction rate, high price, etc., and achieve the effect of no carcinogens, high reduction efficiency, and quality improvement.
- Summary
- Abstract
- Description
- Claims
- Application Information
AI Technical Summary
Problems solved by technology
Method used
Examples
Embodiment 1
[0025] When in the technology of molten metal, sign to the situation of lead-free tin with high silver content, the parts by weight of various compositions of the present invention are as follows: polyoxyethylene ether nonylphenol phosphate ester 55 parts, ammonium dihydrogen phosphate 30 parts, 10 parts of ammonium hydroxysuccinate. The production process of the present invention comprises the following steps: first, take out the polyoxyethylene ether nonylphenol phosphate, ammonium dihydrogen phosphate and ammonium hydroxysuccinate in the above-mentioned weight ratio as required. In this embodiment, the specific weight is 55 kg of polyoxyethylene ether nonylphenol phosphate, 30 kg of ammonium dihydrogen phosphate, and 10 kg of ammonium hydroxysuccinate; first heat polyoxyethylene ether nonylphenol phosphate to 180°C, and then add hydroxysuccinate ammonium Stir slowly until it is completely dissolved, then cool; after cooling, slowly add ammonium dihydrogen phosphate and stir...
Embodiment 2
[0029] Embodiment 2: This embodiment is still the case of lead-free tin with high silver content, and its optimized process formula is: 60 parts of polyoxyethylene ether nonylphenol phosphate, 35 parts of ammonium dihydrogen phosphate, 5 parts of ammonium hydroxysuccinate share. In this embodiment, the specific weight ratio is: 60 kg of polyoxyethylene ether nonylphenol phosphate, 35 kg of ammonium dihydrogen phosphate, and 5 kg of ammonium hydroxysuccinate.
[0030] Other parts of this embodiment are identical to Embodiment 1.
Embodiment 3
[0031] Embodiment 3: This embodiment is still another preferred process formula for the situation of high silver content lead-free tin: 65 parts of polyoxyethylene ether nonylphenol phosphate, 27 parts of ammonium dihydrogen phosphate, ammonium hydroxysuccinate 2 servings. In this embodiment, the specific weight ratio is: 65 kg of polyoxyethylene ether nonylphenol phosphate, 27 kg of ammonium dihydrogen phosphate, and 2 kg of ammonium hydroxysuccinate.
[0032] Other parts of this embodiment are identical to Embodiment 1.
PUM
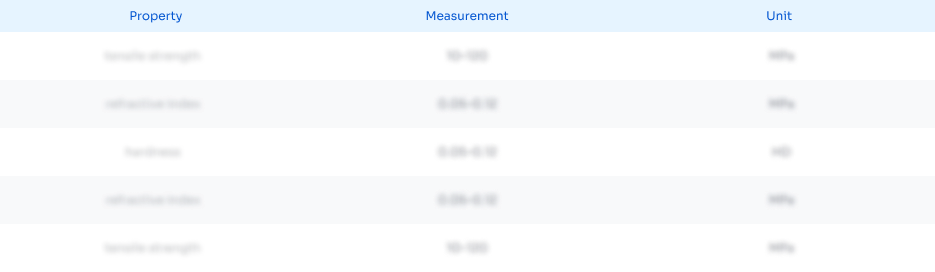
Abstract
Description
Claims
Application Information

- R&D
- Intellectual Property
- Life Sciences
- Materials
- Tech Scout
- Unparalleled Data Quality
- Higher Quality Content
- 60% Fewer Hallucinations
Browse by: Latest US Patents, China's latest patents, Technical Efficacy Thesaurus, Application Domain, Technology Topic, Popular Technical Reports.
© 2025 PatSnap. All rights reserved.Legal|Privacy policy|Modern Slavery Act Transparency Statement|Sitemap|About US| Contact US: help@patsnap.com