Die-pressing processing method for bar coils of motor
A strip coil, molded processing technology, applied in the direction of laying solid insulation, etc., can solve the problems of affecting the appearance quality and insulation quality, insulation breakdown to the ground, and poor size guarantee, so as to shorten the production cycle, enhance the insulation strength, Effect of reducing volume and weight
- Summary
- Abstract
- Description
- Claims
- Application Information
AI Technical Summary
Problems solved by technology
Method used
Image
Examples
Embodiment 1
[0033] A molding process method for strip coils of electric motors. The coils are transposed from the strip coil straight to the end 2 / 3, and the lead wires are sealed and welded. processing and molding process,
[0034] 1) Wrap the main insulation
[0035] a Place the upper and lower layer strip coils on the coil support of the wrapping machine respectively;
[0036] b. Adjust the geometric shape and size of the end of the wrapping machine, and install the required end lifting pads at the end of the wrapping machine to avoid distortion and deformation of the geometric rising angle of the end when the main insulation is wrapped;
[0037] c Carry out the main insulation wrapping according to the compression amount given by the process; when wrapping the main insulation, adjust the running speed of the taping machine at the R corner of the wrapping end to ensure that 1 / 2 half of the mica tape is wound flat and evenly, avoiding inner corners Thickened, the half-stacked winding ...
PUM
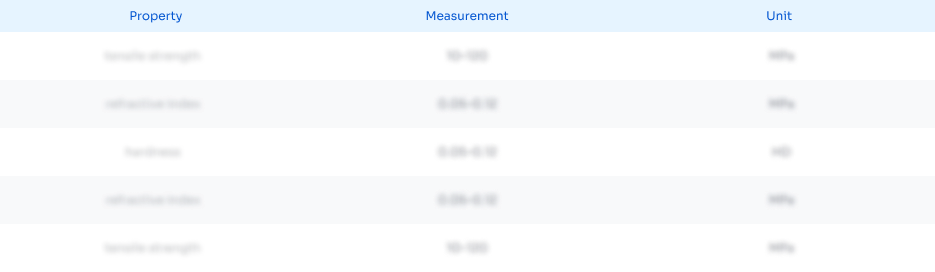
Abstract
Description
Claims
Application Information

- R&D
- Intellectual Property
- Life Sciences
- Materials
- Tech Scout
- Unparalleled Data Quality
- Higher Quality Content
- 60% Fewer Hallucinations
Browse by: Latest US Patents, China's latest patents, Technical Efficacy Thesaurus, Application Domain, Technology Topic, Popular Technical Reports.
© 2025 PatSnap. All rights reserved.Legal|Privacy policy|Modern Slavery Act Transparency Statement|Sitemap|About US| Contact US: help@patsnap.com