Thumb mechanism of underactuated self-adaptive hand prosthesis
An underactuated, self-adaptive technology applied in the field of anthropomorphic manipulators
- Summary
- Abstract
- Description
- Claims
- Application Information
AI Technical Summary
Problems solved by technology
Method used
Image
Examples
specific Embodiment approach 1
[0005] Specific embodiment one: (see Figure 1~Figure 8 ) This embodiment consists of an under-driving mechanism of the thumb and a transmission mechanism of the thumb. The under-driving mechanism of the thumb consists of a thumb fingertip sleeve 1, a lower thumb cover 2, a right thumb plate 3, a thumb upper cover 11, and a fingertip spring. 12. Thumb fingertip shaft 13, torque sensor 20, fingertip 27, thumb link 28, thumb left plate 30, thumb fingertip pin sleeve 32, thumb link pin 33, thumb fingertip link pin 37, The thumb spring stop pin 38, the ball hinge 42, and the ball hinge connecting rod pin 46 are composed. The thumb fingertip shaft 13 is set at the upper end between the thumb right plate 3 and the thumb left plate 30, and the lower end of the fingertip 27 is set on the thumb On the fingertip shaft 13, the thumb fingertip sleeve 1 is fixed on the fingertip 27, the thumb spring stop pin 38 is fixed on the inner upper end of the right thumb plate 3, the fingertip spring 12 ...
specific Embodiment approach 2
[0006] Specific implementation manner two: (see figure 1 , Picture 9 ) This embodiment is different from the first embodiment in that it adds a thumb elastic cover 31, one end of the thumb elastic cover 31 is fixed on the outer surface of the thumb upper cover 11, and the other end of the thumb elastic cover 31 It is frictionally connected with the outer surface of the thumb fingertip sleeve 1. The other composition and connection relationship are the same as in the first embodiment. The function of the added thumb elastic cover plate 31 is to protect the transmission mechanism inside the thumb from being exposed, prevent foreign objects from entering, and affect the service life.
[0007] Working principle: the output shaft of the motor 40 drives the thumb motor pulley 48 to rotate, drives the thumb reducer pulley 10 to rotate, the thumb reducer pulley 10 drives the wave generator shaft 54 to rotate, and the wave generator shaft 54 drives the harmonic gear reducer The wave ...
PUM
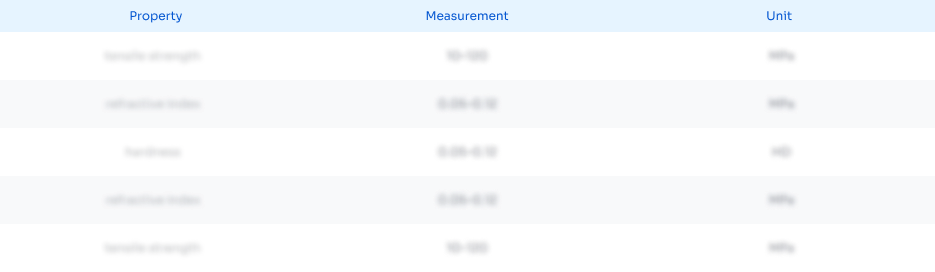
Abstract
Description
Claims
Application Information

- R&D
- Intellectual Property
- Life Sciences
- Materials
- Tech Scout
- Unparalleled Data Quality
- Higher Quality Content
- 60% Fewer Hallucinations
Browse by: Latest US Patents, China's latest patents, Technical Efficacy Thesaurus, Application Domain, Technology Topic, Popular Technical Reports.
© 2025 PatSnap. All rights reserved.Legal|Privacy policy|Modern Slavery Act Transparency Statement|Sitemap|About US| Contact US: help@patsnap.com