Injection molding process
A technology of injection molding process and process steps, applied in the direction of coating, etc., can solve the problems of affecting plastic fluidity, complex process, poor mechanical properties at weld lines, etc., and achieve good internal structure consistency, high surface brightness, and mechanical properties excellent effect
- Summary
- Abstract
- Description
- Claims
- Application Information
AI Technical Summary
Problems solved by technology
Method used
Image
Examples
Embodiment Construction
[0008] Now set forth the present invention in detail in conjunction with accompanying drawing:
[0009] The injection molding process steps of this embodiment are: 1) soften the water first, and steam it through a steam boiler; 2) send water vapor to the water channel in the mold through the control of the valve controller, so that the mold is heated to a temperature close to the melting temperature of the plastic and kept warm; 3) Inject high-temperature molten plastic into the mold; 4) After the molten plastic fills the entire mold cavity, the valve controller turns off the delivery of water vapor and transfers cooling water to the water channel to cool the mold; 5) Open the mold to take the finished product.
[0010] The embodiments described above are only preferred embodiments of the present invention, and are not intended to limit the scope of the present invention. Therefore, all equivalent changes made according to the principle of the present invention should be covere...
PUM
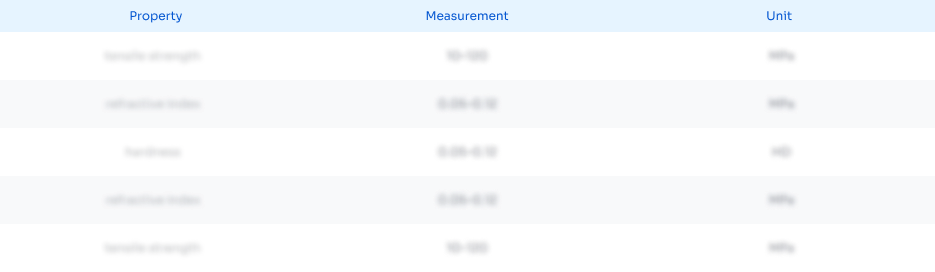
Abstract
Description
Claims
Application Information

- R&D
- Intellectual Property
- Life Sciences
- Materials
- Tech Scout
- Unparalleled Data Quality
- Higher Quality Content
- 60% Fewer Hallucinations
Browse by: Latest US Patents, China's latest patents, Technical Efficacy Thesaurus, Application Domain, Technology Topic, Popular Technical Reports.
© 2025 PatSnap. All rights reserved.Legal|Privacy policy|Modern Slavery Act Transparency Statement|Sitemap|About US| Contact US: help@patsnap.com