Preparation process of copper pipe material for electronic thermotubes
A preparation process and heat pipe technology, which is applied in the field of preparation process of copper tube materials for electronic heat pipes, can solve problems such as difficult processes, and achieve the effects of meeting customer needs, reducing process processing, and reducing production costs
- Summary
- Abstract
- Description
- Claims
- Application Information
AI Technical Summary
Problems solved by technology
Method used
Examples
Embodiment 1
[0009] A straight tube of hard heat pipe material, the specification is φ6X0.30mm, the allowable deviation of outer diameter is ±0.03mm, the allowable deviation of wall thickness is ±0.02mm, Rm≥320Mpa, Hv: 105-130, straightness <12mm / 3000mm;
[0010] 1. Melting and casting: use vacuum induction furnace for melting and casting, melting temperature: 1150~1250℃, casting speed: 2.5~3.5m / h, cast into an ingot of φ245mm specification.
[0011] 2. Extrusion: use an extruder to perform water seal peeling and extrude the ingot with a matching mandrel. The extrusion process is heating temperature: 740 ~ 880 ℃, extrusion speed: 35 ~ 50mm / s, extrusion ratio: 21 , Pressure residual thickness: 25 ~ 40mm, extruded into a tube blank of φ80X10mm.
[0012] 3. Sawing: Use a sawing machine to cut the head and tail of the extruded tube blank.
[0013] 4. Straightening: Use horizontal straightening to straighten the sawed tube blank.
[0014] 5. Rolling: Use the tube rolling mill to roll the stra...
Embodiment 2
[0021] A straight tube of hard heat pipe material, the specification is φ6X0.30mm, the allowable deviation of outer diameter is ±0.03mm, the allowable deviation of wall thickness is ±0.02mm, Rm≥320Mpa, Hv: 105-130, straightness <12mm / 3000mm;
[0022] 1. Melting and casting: use coreless vacuum induction furnace for melting and casting, melting temperature: 1150~1250℃, casting speed: 2.5~3.5m / h, cast into an ingot of φ245mm specification.
[0023] 2. Extrusion: use an extruder to perform water seal peeling and extrude the ingot with a matching mandrel. The extrusion process is heating temperature: 740 ~ 880 ℃, extrusion speed: 35 ~ 50mm / s, extrusion ratio: 21 , Pressure residual thickness: 25 ~ 40mm, extruded into a tube blank of φ80X10mm.
[0024] 3. Sawing: Use the sawing equipment attached to the extruder to cut the head and tail of the extruded tube blank.
[0025] 4. Straightening: Use horizontal straightening to straighten the sawed tube blank.
[0026] 5. Rolling: Use ...
Embodiment 3
[0033] A straight tube of hard heat pipe material, specification φ6X0.30mm, allowable deviation of outer diameter ±0.03mm, allowable deviation of wall thickness ±0.02mm, Rm≥320Mpa, Hv: 105-130, straightness <12mm / 3000mm.
[0034] 1. Melting and casting: use cored vacuum induction furnace for melting and casting, melting temperature: 1150~1250℃, casting speed: 2.5~3.5m / h, cast into an ingot of φ245mm specification.
[0035] 2. Extrusion: use an extruder to perform water seal peeling and extrude the ingot with a matching mandrel. The extrusion process is heating temperature: 740 ~ 880 ℃, extrusion speed: 35 ~ 50mm / s, extrusion ratio: 21 , Pressure residual thickness: 25 ~ 40mm, extruded into a tube blank of φ80X10mm.
[0036] 3. Sawing: Use the sawing equipment attached to the extruder to cut the head and tail of the extruded tube blank.
[0037] 4. Straightening: Use horizontal straightening to straighten the sawed tube blank.
[0038] 5. Rolling: Use the tube rolling mill to r...
PUM
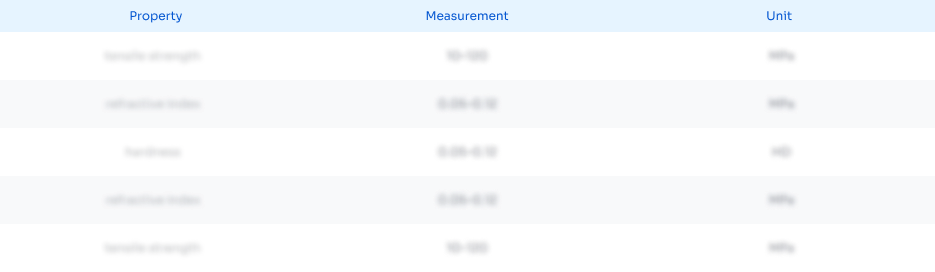
Abstract
Description
Claims
Application Information

- R&D Engineer
- R&D Manager
- IP Professional
- Industry Leading Data Capabilities
- Powerful AI technology
- Patent DNA Extraction
Browse by: Latest US Patents, China's latest patents, Technical Efficacy Thesaurus, Application Domain, Technology Topic, Popular Technical Reports.
© 2024 PatSnap. All rights reserved.Legal|Privacy policy|Modern Slavery Act Transparency Statement|Sitemap|About US| Contact US: help@patsnap.com