Method for recovering medium-concentration and low-concentration vanadium in industrial sewage resulted from stone coal vanadium extraction
A technology of industrial wastewater and recovery method is applied in the field of recovery of low-concentration vanadium in industrial wastewater of vanadium extraction from stone coal, and achieves the effects of alleviating environmental pollution, reducing concentration, and reducing the concentration of vanadium.
- Summary
- Abstract
- Description
- Claims
- Application Information
AI Technical Summary
Problems solved by technology
Method used
Image
Examples
example 1
[0028] Take 100ml of waste water for extracting vanadium from stone coal with a vanadium ion concentration of 1mg / L, add 0.05mg of sodium chlorate to oxidize the low-valent vanadium in the solution to pentavalent vanadium. Adjust the pH value of the solution to 3.0 with ammonia water with a mass fraction of 18-25%, add 3ml TritonX-114, place it in a 45°C water bath and heat for 10min to fully dissolve it. Centrifuge the phases in a centrifuge for 10 minutes while it is hot, and the vanadium ions are enriched in the micellar phase of the surfactant. Add 5ml of sulfuric acid solution with a mass fraction of 10% to the surfactant micelles that come out after phase separation, and heat to 45°C in a water bath again to fully dissolve it. The phases were separated by centrifugation for 10 min while hot. The recovery rate of vanadium was 91.6%. The vanadium-containing enrichment solution obtained by stripping can be returned to the vanadium extraction and leaching process of stone ...
example 2
[0030] Get 100ml of vanadium-extracting wastewater from stone coal containing 5mg / L of vanadium, add 0.17mg of sodium chlorate to oxidize the low-valent vanadium in the solution to pentavalent vanadium. Adjust the pH value of the solution to 3.0 with a mass fraction of 18-25%, add 4ml TritonX-114, place in a 50°C water bath and heat for 15min to fully dissolve it. Centrifuge the phases in a centrifuge for 15 minutes while hot, and the vanadium ions are enriched in the micellar phase of the surfactant. Add 5ml of sulfuric acid solution with a mass fraction of 10% to the surfactant micelles after phase separation, and heat to 50°C in a water bath again to fully dissolve it. The phases were separated by centrifugation for 15 min while hot. The recovery rate of vanadium was 82.1%. The vanadium-containing enrichment solution obtained by stripping can be returned to the vanadium extraction and leaching process of stone coal, and the separated surfactant can be recycled.
example 3
[0032] Take 100ml of vanadium-extracting wastewater from stone coal containing 10mg / L of vanadium, add 0.40mg of sodium hypochlorite to oxidize the low-valent vanadium in the solution to pentavalent vanadium. Adjust the pH value of the solution to 3.5 by using ammonia water with a mass fraction of 18-25%, add 5ml TritonX-114, place it in a water bath at 60°C and heat it for 20min to fully dissolve it. Centrifuge the phases in a centrifuge for 15 minutes while hot, and the vanadium ions are enriched in the micellar phase of the surfactant. Add 5ml of sulfuric acid solution with a mass fraction of 10% to the surfactant micelles after phase separation, and heat to 60° C. in a water bath again to fully dissolve it. The phases were separated by centrifugation for 15 min while hot. The recovery rate of vanadium is 76.1.3%. The vanadium-containing enrichment solution obtained by stripping can be returned to the vanadium extraction and leaching process of stone coal, and the separat...
PUM
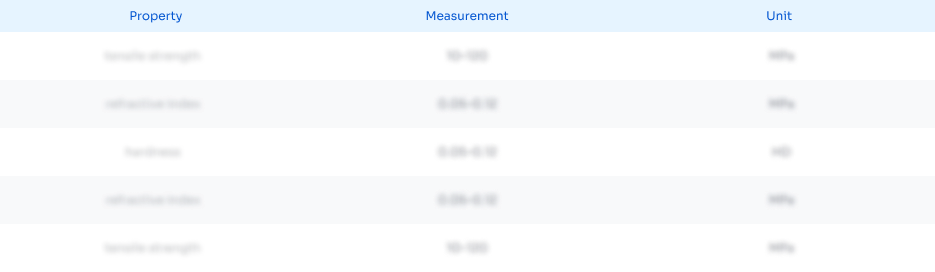
Abstract
Description
Claims
Application Information

- Generate Ideas
- Intellectual Property
- Life Sciences
- Materials
- Tech Scout
- Unparalleled Data Quality
- Higher Quality Content
- 60% Fewer Hallucinations
Browse by: Latest US Patents, China's latest patents, Technical Efficacy Thesaurus, Application Domain, Technology Topic, Popular Technical Reports.
© 2025 PatSnap. All rights reserved.Legal|Privacy policy|Modern Slavery Act Transparency Statement|Sitemap|About US| Contact US: help@patsnap.com