Method for preparing high metallic texture high transmission lens
A technology with high metal texture, applied in metal material coating technology, optics, optical components, etc., can solve the problem of plastic lenses with poor wear resistance, scratch resistance, environmental temperature resistance, acid and alkali corrosion, etc. Plastic lenses do not have good metal texture and other problems, so as to achieve the effect of strong metal texture and high light transmittance
- Summary
- Abstract
- Description
- Claims
- Application Information
AI Technical Summary
Problems solved by technology
Method used
Examples
Embodiment 1
[0020] The product to be coated is subjected to five layers of optical coating in the optical coating device: the first layer of Tio 2 Coating, second layer SiO 2 Coating, the third layer of TiO 2 Coating, fourth layer SiO 2 Coating, the fifth layer of TiO 2 coating.
[0021] The optical coating device includes a vacuum coating chamber, 2 crucibles and 2 electron guns. Before coating, put the product to be coated into the vacuum coating chamber, seal the vacuum coating chamber, and vacuum the vacuum coating chamber to achieve a vacuum pressure of 3.0×10 -3 Stop vacuuming after pa. Inflate the vacuum coating chamber with an oxygen flow rate of 15 sccm, an argon flow rate of 8 sccm, and a vacuum pressure of 1.5×10 -2 pa. When the coating starts, the current of the ion source in the vacuum coating chamber is 3A, and the ion source plays the role of assisting the evaporation of the crucible evaporation source to enhance the effect of optical coating.
[0022] The 2 crucibl...
Embodiment 2
[0026] The difference between this embodiment and embodiment 1 is:
[0027] In an environment with a temperature of 20°C and a humidity of 50%, put the optically coated product on the automatic line of the No. 1 coating machine, and the line speed of the No. 1 coating machine is 20Hz. Carry out pre-treatment wiping and automatic electrostatic dust removal to remove dust, traces, impurities and other impurities on the product, inject the primer numbered ENPLAPRIMER and paint viscosity of 8s into the ion air gun, and the air pressure of the ion air gun is 2.75kg / cm 2 , carry out automatic spraying, spray the primer onto the coated surface of the product, the film thickness of the sprayed coating is 6um, put the coated product into an infrared oven for baking, the temperature of the infrared oven is 45°C, and the baking time is 13min.
[0028] In an environment with a temperature of 20°C and a humidity of 50%, the product after spraying the bottom layer of the primer is placed on...
Embodiment 3
[0031] The difference between this embodiment and embodiment 1 is:
[0032] In an environment with a temperature of 35°C and a humidity of 80%, put the optically coated product on the automatic line of the No. 1 coating machine, and the line speed of the No. 1 coating machine is 20Hz. Carry out pre-treatment wiping and automatic electrostatic dust removal to remove dust, traces, impurities and other impurities on the product, inject the primer numbered ENPLAPRIMER and paint viscosity of 10s into the ion air gun, and the air pressure of the ion air gun is 3.5kg / cm 2 , carry out automatic spraying, spray the primer onto the coated surface of the product, the film thickness of the sprayed coating is 7um, put the coated product into an infrared oven for baking, the temperature of the infrared oven is 50°C, and the baking time is 15min.
[0033] In an environment with a temperature of 35°C and a humidity of 80%, the product after spraying the bottom layer of the primer is placed on...
PUM
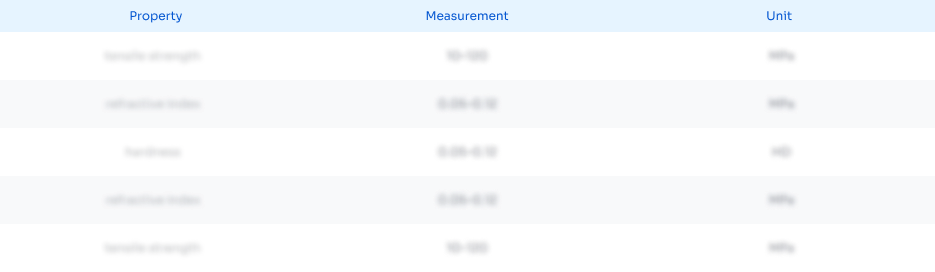
Abstract
Description
Claims
Application Information

- Generate Ideas
- Intellectual Property
- Life Sciences
- Materials
- Tech Scout
- Unparalleled Data Quality
- Higher Quality Content
- 60% Fewer Hallucinations
Browse by: Latest US Patents, China's latest patents, Technical Efficacy Thesaurus, Application Domain, Technology Topic, Popular Technical Reports.
© 2025 PatSnap. All rights reserved.Legal|Privacy policy|Modern Slavery Act Transparency Statement|Sitemap|About US| Contact US: help@patsnap.com