Method for preparing solid phase of chlorinated polypropylene or chlorinated maleic anhydride inoculated polypropylene
A technology of chlorinated polypropylene and grafted polypropylene is applied in the field of solid-phase preparation of chlorinated polypropylene and chlorinated maleic anhydride grafted polypropylene, which can solve the problem of uneven reaction, easy coking of products and adhesion and grafting. problems such as low branch rate, to achieve the effect of improving the uniformity of chlorination, low production cost and controllable chlorine content
- Summary
- Abstract
- Description
- Claims
- Application Information
AI Technical Summary
Problems solved by technology
Method used
Examples
Embodiment 1
[0018] Add 100 parts by weight of polypropylene particles into a reaction kettle with a stirring device, heat up to 70°C under stirring, feed chlorine gas into the reaction kettle for 6 hours, drive away the chlorine gas in the reaction kettle with clean air, and transfer the material to a ball mill Crumble for 0.5h; then add the crushed powder and 1 weight part of azobisisobutyronitrile into the reactor, heat up to 70°C under stirring, and pass in chlorine gas for secondary chlorination. After 2 hours of reaction, stop Heating, using clean air to drive away the chlorine in the kettle, the chlorination product is washed with water to neutralize the acid, and after drying, chlorinated polypropylene with a chlorine content of 23.47% by weight can be obtained.
Embodiment 2
[0020] Add 100 parts by weight of polypropylene particles and 1 part by weight of azobisisobutyronitrile into a reaction kettle with a stirring device. Heat up to 80°C under stirring, and react with chlorine gas for 4 hours, drive away the chlorine gas in the reactor with clean air, transfer the material to a ball mill for crushing for 0.5 hour, and then crush the crushed powder, azobisisobutyronitrile Add 1 part by weight into the reaction kettle, heat up to 80°C under stirring, pass in chlorine gas for secondary chlorination, stop heating after 4 hours of reaction, drive away the chlorine gas in the kettle with clean air, and wash the chlorinated product with water After deacidification to neutrality, chlorinated polypropylene with a chlorine content of 28.48% by weight can be obtained after drying.
Embodiment 3
[0022] Add 100 parts by weight of polypropylene particles and 1 part by weight of azobisisobutyronitrile into a reaction kettle with a stirring device. Heat up to 90°C under stirring, and react with chlorine gas for 2 hours, drive away the chlorine gas in the reaction kettle with clean air, and transfer the material to a ball mill for crushing for 0.5 hour. Then add the crushed powder and 1 part by weight of azobisisobutyronitrile into the reaction kettle, heat up to 90° C. under stirring, and pass in chlorine gas for secondary chlorination. After reacting for 5 hours, the heating was stopped, and the chlorine gas in the kettle was driven away with clean air, and the chlorinated product was washed with water to neutralize the acid, and after drying, chlorinated polypropylene with a chlorine content of 30.33% by weight was obtained.
PUM
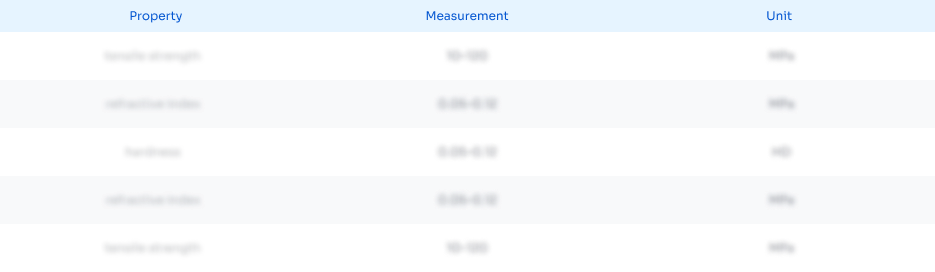
Abstract
Description
Claims
Application Information

- R&D
- Intellectual Property
- Life Sciences
- Materials
- Tech Scout
- Unparalleled Data Quality
- Higher Quality Content
- 60% Fewer Hallucinations
Browse by: Latest US Patents, China's latest patents, Technical Efficacy Thesaurus, Application Domain, Technology Topic, Popular Technical Reports.
© 2025 PatSnap. All rights reserved.Legal|Privacy policy|Modern Slavery Act Transparency Statement|Sitemap|About US| Contact US: help@patsnap.com