Process and equipment for negative pressure benzene removal
A debenzene and negative pressure technology, which is applied in the petroleum industry, combustible gas purification, combustible gas purification/reconstruction, etc., can solve the problems of high production consumption, low recovery rate, low quality, etc., and achieve the effect of reducing energy consumption
- Summary
- Abstract
- Description
- Claims
- Application Information
AI Technical Summary
Problems solved by technology
Method used
Image
Examples
Embodiment 1
[0026] Embodiment 1, a kind of negative pressure debenzene method, it comprises tower body, debenzene tower rich oil inlet 21, tower top gas phase outlet 16, light benzene return flow port 17, heavy benzene outlet 18, naphthalene oil outlet 19, lean oil The debenzene tower 2 that exports 25 etc. forms, and its flow process is:
[0027] (1) Use the vacuum pump 7 to pump air so that the pressure of the oil-rich debenzene and oil washing regeneration system is a negative pressure of 0.06-0.07Mpa,
[0028] (2) The temperature of the rich oil from the benzene washing section is ~30°C, and the temperature of the hot lean oil from the debenzene tower 2 is raised to 180-200°C through the lean-rich oil heat exchanger 1 and enters the stripping section of the debenzene tower ;
[0029] (3) The temperature of the light benzene vapor obtained at the top of the debenzene tower is 40-45°C, and after being condensed by the condenser 6, oil-water separation is carried out through the oil-wat...
Embodiment 2
[0033] Embodiment 2, a negative pressure debenzene method, which comprises a tower body, a debenzene tower rich oil inlet 21, a gas phase outlet 16 at the top of the tower, a light benzene return port 17, a heavy benzene outlet 18, a naphthalene oil outlet 19, and a lean oil The debenzene tower 2 that exports 25 etc. forms, and its flow process is:
[0034] (1) Use the vacuum pump 7 to pump air so that the pressure of the oil-rich debenzene and oil washing regeneration system is a negative pressure of 0.06-0.07Mpa,
[0035] (2) The temperature of the rich oil from the benzene washing section is ~30°C, and the temperature of the lean oil from the debenzene tower 2 is raised to 150°C through the lean-rich oil heat exchanger 1, and then enters the debenzene tubular heating furnace 3 The convection section continues to heat up to 180-200°C and enters the stripping section of the debenzene tower;
[0036] (3) The temperature of the light benzene vapor obtained at the top of the de...
Embodiment 3
[0040] Embodiment 3 The debenzene tower disclosed by the present invention is a variable-diameter tower whose lower part is a thicker stripping section 47 with a diameter, the middle is a tapered transition section 45, and the upper part is a thinner rectification section 42. The diameter ratio of the distillation section is 1:0.7-1, the oval head 41 at the top of the rectification section is equipped with a gas phase outlet 16 at the top of the tower, and at least 10 layers of PFG4.5 structured packing 44 and KCF gas-liquid distributor are installed in the rectification section 43. The tower body is provided with a light benzene return port 17, a heavy benzene outlet 18, and a naphthalene oil outlet 19; 19 layers of anti-clogging IV oblique hole double overflow trays 46 are installed in the stripping section, and the downcomer of adjacent trays The directions of the grooves are perpendicular to each other. The tower body is provided with a rich oil inlet 21, a regeneration oil...
PUM
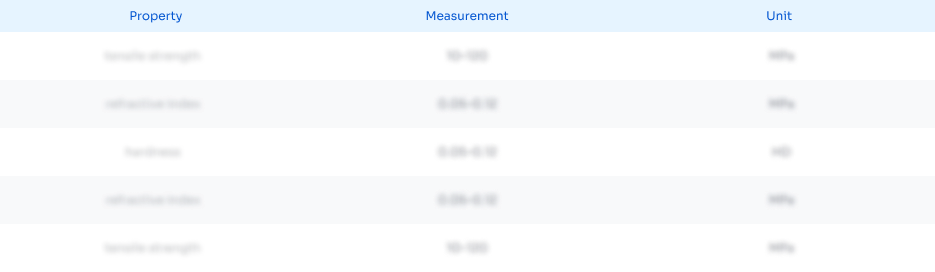
Abstract
Description
Claims
Application Information

- R&D
- Intellectual Property
- Life Sciences
- Materials
- Tech Scout
- Unparalleled Data Quality
- Higher Quality Content
- 60% Fewer Hallucinations
Browse by: Latest US Patents, China's latest patents, Technical Efficacy Thesaurus, Application Domain, Technology Topic, Popular Technical Reports.
© 2025 PatSnap. All rights reserved.Legal|Privacy policy|Modern Slavery Act Transparency Statement|Sitemap|About US| Contact US: help@patsnap.com