A method for manufacturing modified extra fine heavy calcium carbonate powder
A technology of heavy calcium carbonate powder and manufacturing method, applied in chemical instruments and methods, inorganic pigment treatment, dyeing physical treatment, etc. Shear viscosity, inability to improve the washing resistance of the coating, etc., to achieve the effect of increasing the washing resistance, increasing the high shear viscosity, and improving the hydrophobicity
- Summary
- Abstract
- Description
- Claims
- Application Information
AI Technical Summary
Problems solved by technology
Method used
Examples
Embodiment 1
[0008] Put 10 tons of calcite with a diameter of less than 20 cm into the jaw crusher continuously for crushing, and the crushed small stones enter the hammer crusher for crushing to obtain calcium carbonate coarse material less than 5 mm and enter the coarse material bin; set up above the entrance of the grinder A water tank, add 10 kilograms of polyethylene glycol and 10 kilograms of pure water in the water tank, install a stirrer in the water tank, make the polyethylene glycol and water mix evenly, connect a flow meter with a switch under the water tank, The flow meter is used to control and display the flow rate of polyethylene glycol and water mixture. The bottom of the flow meter is connected to the water pipe. The water pipe introduces the mixed liquid passing through the flow meter to the entrance of the grinder; the coarse calcium carbonate is uniformly distributed through the feeder The mixed liquid of 10 kg polyethylene glycol and 10 kg water meets at the feed inlet ...
Embodiment 2
[0010] Put 10 tons of calcite with a diameter of less than 20 cm into the jaw crusher continuously for crushing, and the crushed small stones enter the hammer crusher for crushing to obtain calcium carbonate coarse material less than 5 mm and enter the coarse material bin; set up above the entrance of the grinder A water tank, add 100 kilograms of polyethylene glycol and 100 kilograms of pure water in the water tank, install a stirrer in the water tank, make the polyethylene glycol and water mix evenly, connect a flow meter with a switch under the water tank, The flow meter is used to control and display the flow rate of polyethylene glycol and water mixture. The bottom of the flow meter is connected to the water pipe. The water pipe introduces the mixed liquid passing through the flow meter to the entrance of the grinder; the coarse calcium carbonate is uniformly distributed through the feeder The mixed liquid of 100 kg polyethylene glycol and 100 kg water meets at the feed in...
PUM
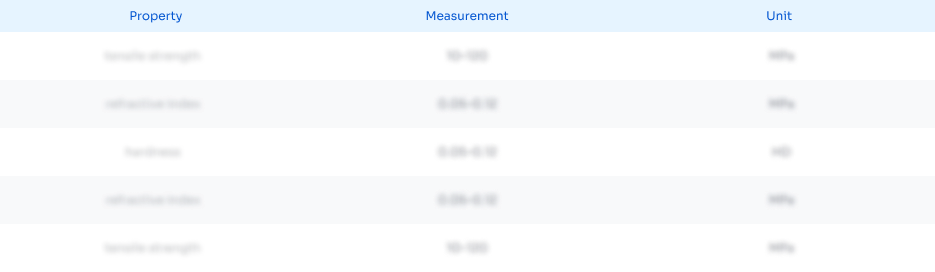
Abstract
Description
Claims
Application Information

- R&D
- Intellectual Property
- Life Sciences
- Materials
- Tech Scout
- Unparalleled Data Quality
- Higher Quality Content
- 60% Fewer Hallucinations
Browse by: Latest US Patents, China's latest patents, Technical Efficacy Thesaurus, Application Domain, Technology Topic, Popular Technical Reports.
© 2025 PatSnap. All rights reserved.Legal|Privacy policy|Modern Slavery Act Transparency Statement|Sitemap|About US| Contact US: help@patsnap.com