Fiber grating strain and temperature simultaneously measuring sensor
A technology for measuring sensors and strain sensors, applied in the field of engineering structural strain and temperature measuring devices, can solve the problems of inability to meet the requirements of integration of structural monitoring sensors, complex wires, signal distortion, etc., and achieve strong anti-electromagnetic interference ability and long-term stability. Good performance and little impact on structure
- Summary
- Abstract
- Description
- Claims
- Application Information
AI Technical Summary
Problems solved by technology
Method used
Image
Examples
Embodiment Construction
[0018] The technical scheme of the present invention is described in detail below in conjunction with accompanying drawing:
[0019] Such as Figure 1 to Figure 4 As shown, the optical fiber grating strain of the present invention, the temperature simultaneously measuring sensor comprises the first pigtail 1; The first stainless steel tube 2; The first epoxy resin 3; The second pigtail 4; The third pigtail 5; The second stainless steel tube 6; the second epoxy resin 7; the first bare fiber grating 8; the third epoxy resin 9; the metal tube 10; the fourth epoxy resin 11; the second bare fiber grating 12, heat-conducting liquid 13; The tube 6 was cleaned and dried with alcohol and then fixed on the experimental platform. The coating layer was removed from the grating section of the first bare fiber grating 8 and wiped with absorbent cotton ball dipped in alcohol, and then passed through the second stainless steel tube 6 to form a first Pigtail 1 and the second pigtail 4, adjust...
PUM
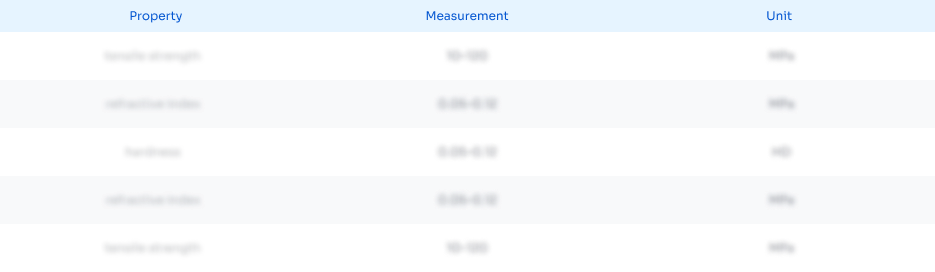
Abstract
Description
Claims
Application Information

- Generate Ideas
- Intellectual Property
- Life Sciences
- Materials
- Tech Scout
- Unparalleled Data Quality
- Higher Quality Content
- 60% Fewer Hallucinations
Browse by: Latest US Patents, China's latest patents, Technical Efficacy Thesaurus, Application Domain, Technology Topic, Popular Technical Reports.
© 2025 PatSnap. All rights reserved.Legal|Privacy policy|Modern Slavery Act Transparency Statement|Sitemap|About US| Contact US: help@patsnap.com