Trichlorosilane differential pressure coupling rectification system and operation method thereof
A technology of trichlorosilane and differential pressure coupling, applied in the field of rectification, can solve the problems of many theoretical plates, high energy consumption of polysilicon, large reflux ratio, etc., to save energy loss, reduce production costs and energy consumption, and reduce energy consumption. The effect of consumption
- Summary
- Abstract
- Description
- Claims
- Application Information
AI Technical Summary
Problems solved by technology
Method used
Image
Examples
example 1
[0028] The operation method of Process A using low pressure distillation tower (2) feed is as follows:
[0029] Such as figure 1 As shown, after the trichlorosilane raw material (1) is separated by the low pressure rectification tower (2), the light component A (9) is divided into reflux material A (11) according to a certain reflux ratio after passing through the condenser (3) at the top of the tower And the produced material A (10), the light-removed liquid A (12) at the bottom of the tower is divided into two parts, and one part enters the tower kettle to condense the reboiler (4) after heating to form a high boiling liquid A (13) and return to the low pressure tower (2) , The other part enters the pressure tower (5) after rectification to form high boiling liquid A (14) at the bottom of the tower, and forms trichlorosilane gas phase A (15) at the top of the tower and enters the heating medium inlet of the condensation reboiler (4) , After providing the required heat for the c...
example 2
[0040] The operation method of process B using pressurized distillation tower (5) feed is as follows:
[0041] Such as figure 2As shown, the operation method of process B is: after the trichlorosilane raw material (1) is separated by the pressurized distillation tower (5), the light component B (19) at the top of the tower enters the condensation reboiler (4) The heating medium inlet of) provides the required heat for the condensing reboiler and becomes the condensate liquid B (23). After passing through the auxiliary condenser (6), part of it is returned to the top of the pressurizing tower (5) and part of it is extracted. The tower kettle light liquid B (21) is heated by the tower kettle reboiler (7) to form reboiled steam (20) and returns to the pressurizing tower (5). The other part uses the pressure difference between the two towers to directly enter the low pressure as the feed The tower (2) performs separation. After the trichlorosilane gas phase B (27) at the top of the lo...
PUM
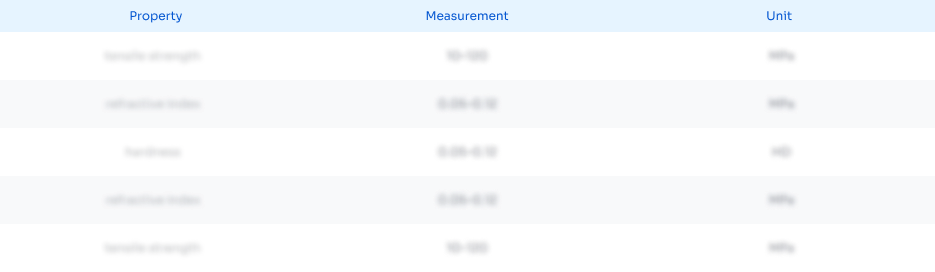
Abstract
Description
Claims
Application Information

- R&D
- Intellectual Property
- Life Sciences
- Materials
- Tech Scout
- Unparalleled Data Quality
- Higher Quality Content
- 60% Fewer Hallucinations
Browse by: Latest US Patents, China's latest patents, Technical Efficacy Thesaurus, Application Domain, Technology Topic, Popular Technical Reports.
© 2025 PatSnap. All rights reserved.Legal|Privacy policy|Modern Slavery Act Transparency Statement|Sitemap|About US| Contact US: help@patsnap.com