Semi-solid forming and casting technology of aluminum magnesium alloy pot
A semi-solid forming, aluminum-magnesium alloy technology, applied in the field of semi-solid forming die-casting technology of aluminum-magnesium alloy pots, can solve the problems of fast metal crystallization speed, low yield of finished castings, and foaming on the metal surface, etc., and achieve energy saving Consumption, no casting defects, strong and durable products
- Summary
- Abstract
- Description
- Claims
- Application Information
AI Technical Summary
Problems solved by technology
Method used
Examples
Embodiment Construction
[0022] The present invention will be described in detail below in combination with specific embodiments.
[0023] A semi-solid forming die-casting process for an aluminum-magnesium alloy pot, which is realized by the following process steps:
[0024] A. Melting of aluminum-magnesium alloy materials: Melting of aluminum-magnesium alloy metals is carried out in a melting furnace, and the melting temperature is 700-800°C;
[0025] B. Scoop the aluminum-magnesium alloy solution with a quantitative heat preservation container, and pour the aluminum-magnesium alloy solution into a heat preservation furnace with a temperature of 650-700°C for semi-solid slurry preparation;
[0026] C. Preheat the extrusion casting mold to 180-260°C, and demold it with graphite powder or mold release agent;
[0027] D. Put the prepared semi-solid aluminum-magnesium alloy slurry into the squeeze casting mold, squeeze cast at the extrusion speed of 0.2~0.6mm / s, and the specific pressure is 40~160MPa, a...
PUM
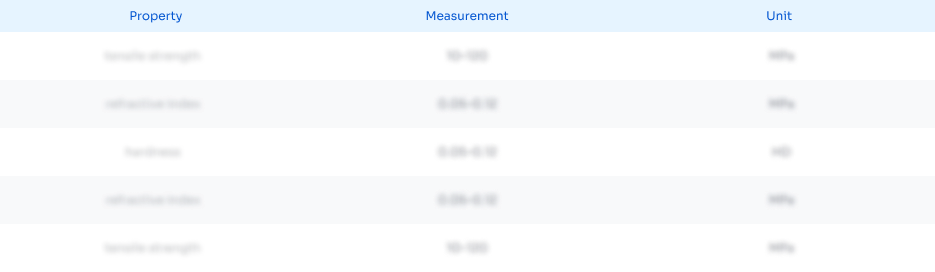
Abstract
Description
Claims
Application Information

- Generate Ideas
- Intellectual Property
- Life Sciences
- Materials
- Tech Scout
- Unparalleled Data Quality
- Higher Quality Content
- 60% Fewer Hallucinations
Browse by: Latest US Patents, China's latest patents, Technical Efficacy Thesaurus, Application Domain, Technology Topic, Popular Technical Reports.
© 2025 PatSnap. All rights reserved.Legal|Privacy policy|Modern Slavery Act Transparency Statement|Sitemap|About US| Contact US: help@patsnap.com