Method for completely reclaiming tail gas of polyethylene device
A technology of polyethylene and tail gas, which is applied in the direction of combined devices, separation methods, chemical instruments and methods, etc., can solve the problems of not reaching zero emissions, and achieve the effect of avoiding emissions
- Summary
- Abstract
- Description
- Claims
- Application Information
AI Technical Summary
Problems solved by technology
Method used
Image
Examples
Embodiment 1
[0032] Example 1: The tail gas temperature after the high-pressure condensate tank of a polyethylene plant in a petrochemical enterprise: -10°C, and pressure: 0.85MpaG. The polyethylene tail gas enters the membrane recovery unit after being heated by steam. First, the raw material gas is pretreated, and the solid particles and liquid droplets contained in the raw material gas are removed through the coarse filter and the fine filter. The temperature is 1.4°C and the pressure is 0.75MpaG. Then enter the two-stage membrane separator, the pressure difference between the front and back of the two-stage membrane is less than 0.1Mpa after separation, there is 464Nm 3 / hr The temperature of permeate gas is 7℃, returning to the compressor inlet of the discharge system, 1271Nm 3 / hr The exhaust gas temperature is 7℃ and enters the buffer tank. The composition of exhaust gas, permeate gas and exhaust gas is shown in the table below.
[0033] Table 2. Exhaust gas condition table of polyethyl...
Embodiment 2
[0043] Example 2: The tail gas temperature after the high-pressure condensate tank of a polyethylene plant in a petrochemical enterprise: -10°C and the raw material gas pressure: 0.9MpaG. After steaming and heating, the polyethylene tail gas enters the membrane recovery system. First, it enters the raw material gas pretreatment, and the solid particles and liquid droplets contained in the raw material are removed through the coarse filter and the fine filter. The temperature is 5°C and the pressure is 0.75MpaG. The pressure difference before and after the exhaust gas passes through the coarse filter and the fine filter is less than 10kpa. Then enter the secondary membrane separator. After separation, the permeate temperature is 5°C and the pressure is 30kpa and returns to the compressor inlet of the discharge system. The exhaust tail gas temperature is 7°C and the pressure is 0.7Mpa and enters the buffer tank. The composition of permeate gas and exhaust gas is shown in the table b...
Embodiment 3
[0051] Example 3: After the tail gas of a high-pressure condensate tank of a polyethylene plant in a petrochemical enterprise is heated by low-pressure steam heating, the temperature: 45°C, and the pressure: 0.85MpaG. The polyethylene tail gas enters the membrane recovery unit. First, the raw material gas is pretreated, and the solid particles and liquid droplets in the raw material gas are removed through the coarse filter and the fine filter. The temperature is 40°C and the pressure is 0.75MpaG. Then enter the secondary membrane separator, after separation, there is 504Nm 3 / hr permeate temperature 37℃, return to the compressor inlet of the discharge system, 1395Nm 3 / hr The exhaust gas temperature is 37℃ and enters the buffer tank. The composition of exhaust gas, permeate gas and exhaust gas is shown in the table below.
[0052] Table 6. Exhaust gas condition table of polyethylene plant of a petrochemical enterprise
[0053]
[0054] Calculating from the above table, the recov...
PUM
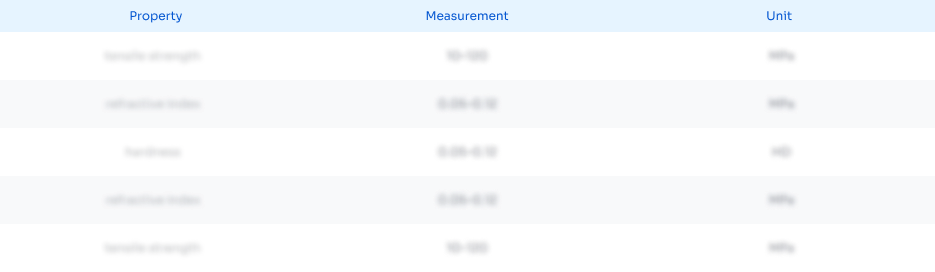
Abstract
Description
Claims
Application Information

- Generate Ideas
- Intellectual Property
- Life Sciences
- Materials
- Tech Scout
- Unparalleled Data Quality
- Higher Quality Content
- 60% Fewer Hallucinations
Browse by: Latest US Patents, China's latest patents, Technical Efficacy Thesaurus, Application Domain, Technology Topic, Popular Technical Reports.
© 2025 PatSnap. All rights reserved.Legal|Privacy policy|Modern Slavery Act Transparency Statement|Sitemap|About US| Contact US: help@patsnap.com