Preparation method of super capacitor plate material
A technology of supercapacitors and plates, applied in capacitor electrodes, capacitor parts, metal material coating processes, etc., can solve problems such as inability to integrate, and achieve the effects of low price, simple operation and low residual amount.
- Summary
- Abstract
- Description
- Claims
- Application Information
AI Technical Summary
Problems solved by technology
Method used
Image
Examples
preparation example Construction
[0034] Concrete preparation method is:
[0035] A. The fabrication process of electrochemical corrosion microchannels based on MEMS technology has been described in detail in patent 200610025900. The main process is to first use photolithography to define the position of the hole in the silicon wafer, perform pre-etching, and stop etching when the hole is in the shape of an inverted square truss; Then, the back side is thinned to the etched position; the unetched part in the middle is separated by ultrasonic separation, and the silicon microchannel (Microchannel P1ate, abbreviated as MCP, silicon microchannel) thrown away from the substrate is obtained. Abbreviated as Si-MCP) structure.
[0036] The etched silicon microchannel SEM photo is as follows figure 1 shown.
[0037] B. Taking the silicon microchannel as a substrate, after surface pretreatment, deposit a nickel layer in an electroless nickel plating solution to make a Ni / Si-MCP (nickel / silicon microchannel) nanocomp...
Embodiment 1
[0041] The silicon microchannel is produced by electrochemical etching of the MEMS process, and the obtained silicon microchannel hole is a square, with a side length of 5 microns, a wall thickness of 1 micron, and a depth of 250 microns. Then use this silicon microchannel as the substrate, before the electroless nickel plating, soak the surface with 1% polyethylene glycol octyl phenyl ether solution for 30 seconds for surface pretreatment, and deposit a nickel layer in the plating solution for 40 minutes to make Ni / Si-MCP nanocomposite structure. Perform rapid thermal annealing on the fabricated Ni / Si-MCP nanocomposite structure. In an oxygen atmosphere, the annealing temperature is controlled at 500°C for 6 to 10 minutes to obtain NiO / Si-MCP (nickel oxide / silicon microchannel) nanostructures. Composite capacitor electrode material, NiO film thickness ℃ is about 500nm.
[0042] Put the prepared NiO / Si-MCP about 1cm 2 The area was used as the working electrode for electroch...
Embodiment 2
[0048] The silicon microchannel is produced by electrochemical etching of the MEMS process, and the obtained silicon microchannel hole is a square, with a side length of 5 microns, a wall thickness of 1 micron, and a depth of 250 microns. Then use this silicon microchannel as the substrate, before the electroless nickel plating, soak the surface with 1% polyethylene glycol octyl phenyl ether solution for 30 seconds for surface pretreatment, and deposit the nickel layer in the plating solution for 30 minutes to make Ni / Si-MCP nanocomposite structure. Perform rapid thermal annealing on the fabricated Ni / Si-MCP nanocomposite structure. In an oxygen atmosphere, the annealing temperature is controlled at 450°C for 6-10 minutes to obtain NiO / Si-MCP (nickel oxide / silicon microchannel) Nano composite capacitor electrode material, NiO film thickness ℃ is about 150nm.
PUM
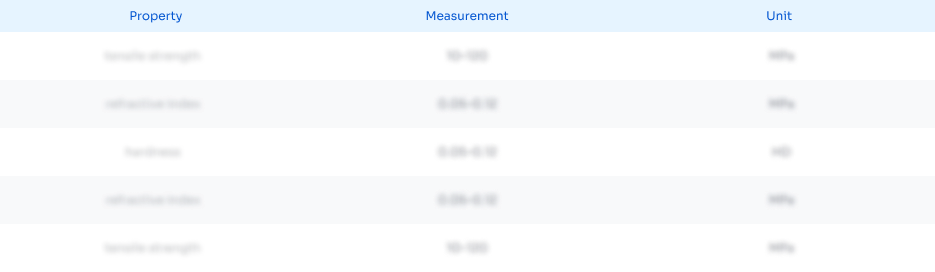
Abstract
Description
Claims
Application Information

- R&D Engineer
- R&D Manager
- IP Professional
- Industry Leading Data Capabilities
- Powerful AI technology
- Patent DNA Extraction
Browse by: Latest US Patents, China's latest patents, Technical Efficacy Thesaurus, Application Domain, Technology Topic, Popular Technical Reports.
© 2024 PatSnap. All rights reserved.Legal|Privacy policy|Modern Slavery Act Transparency Statement|Sitemap|About US| Contact US: help@patsnap.com