Deformation design method for product STL model
A deformation design and model technology, applied in computing, 3D modeling, image data processing, etc., can solve problems such as low efficiency, large amount of deformation calculation, difficult model detail feature editing, etc.
- Summary
- Abstract
- Description
- Claims
- Application Information
AI Technical Summary
Problems solved by technology
Method used
Image
Examples
Embodiment 1
[0032] Example 1: Editing figure 2 The bottom area of the STL model of the Apple product shown, stretching it out of the chassis.
[0033] Such as image 3 As shown in , select the triangular patch in the bottom area of the apple through mouse interaction, and store the vertices p of each triangular patch in the selected area 1 (30.0787, 159.2667, 16.0342), p 2 (29.32109, 159.2667, 16.0475), ..., p k (35.6642, 87.9783, 18.6326), substitute the coordinates of each point into the matrix A, where
[0034] A = x 1 y 1 z 1 1 x 2 ...
Embodiment 2
[0052] Embodiment 2: Setting the local deformation reference surface as a tensor product Bézier surface of degree 4×4, for Image 6 The planar STL model shown is partially edited to form a convex area with the word "TEST", the method is the same as above, and the effect is as follows Figure 7 shown.
Embodiment 3
[0053] Embodiment three: set the local deformation reference surface as a tensor product Bézier surface of degree 4×4, for Figure 8 Edit the STL model of the cow shown, and edit two peaks on the back of the cow STL model, the method is the same as above, and the effect is as follows Figure 9 shown.
PUM
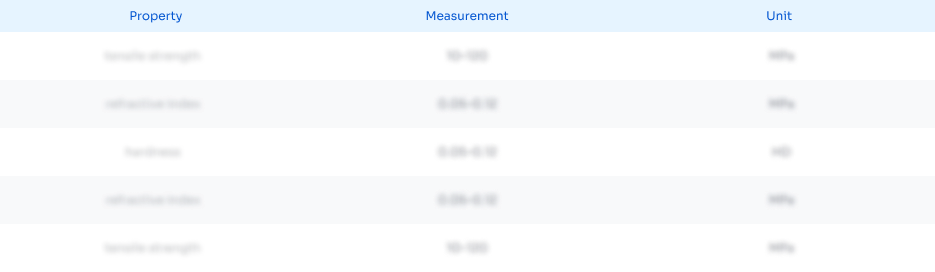
Abstract
Description
Claims
Application Information

- Generate Ideas
- Intellectual Property
- Life Sciences
- Materials
- Tech Scout
- Unparalleled Data Quality
- Higher Quality Content
- 60% Fewer Hallucinations
Browse by: Latest US Patents, China's latest patents, Technical Efficacy Thesaurus, Application Domain, Technology Topic, Popular Technical Reports.
© 2025 PatSnap. All rights reserved.Legal|Privacy policy|Modern Slavery Act Transparency Statement|Sitemap|About US| Contact US: help@patsnap.com