High-light ABS alloy and method for producing the same
An alloy and high-gloss technology is applied in the field of high-gloss ABS alloy and its preparation, which can solve the problems of increasing the total cost of the alloy, high amount of PMMA, low alloy surface hardness, etc., and achieves the effects of low cost, simple preparation process and high impact strength.
- Summary
- Abstract
- Description
- Claims
- Application Information
AI Technical Summary
Problems solved by technology
Method used
Examples
Embodiment 1
[0030] ABS (about 20% rubber content, about 40% styrene content, about 10% acrylonitrile content) weight ratio is 30% (the following are weight ratio), PMMA 30%, AS 25%, toughening agent high rubber powder HR-181 12.5%, black mother UN606 2%, lubricant 0.5%. The mixed material is put into the hopper of the twin-screw extruder, melted and blended, extruded and granulated to form a composite material. Among them, the temperature settings of each heating zone of the screw are as follows: first zone temperature: 185°C; second zone: 195°C; third zone: 200°C; fourth zone: 210°C; fifth zone temperature 210°C; Zone temperature 215°C; machine head: 220°C; residence time 2-3min. The pressure is 15MPa.
Embodiment 2
[0032] ABS (about 26% rubber content, about 45% styrene content, about 15% acrylonitrile content) weight ratio is 40% (the following are weight ratio), PMMA 25%, AS 25%, toughening agent high rubber powder HR-181 7.5%, black masterbatch 2%, lubricant 0.5%. The mixed material is put into the hopper of the twin-screw extruder, melted and blended, extruded and granulated to form a composite material. Among them, the temperature settings of each heating zone of the screw are as follows: first zone temperature: 185°C; second zone: 195°C; third zone: 200°C; fourth zone: 210°C; fifth zone temperature 210°C; Zone temperature 215°C; machine head: 220°C; residence time 2-3min. The pressure is 15MPa.
Embodiment 3
[0034] ABS (about 20% rubber content, about 50% styrene content, about 15% acrylonitrile content) weight ratio is 45% (the following are weight ratio), PMMA 20%, AS 25%, toughening agent high rubber powder HR-181 7.5%, black mother UN606 2%, lubricant 0.5%. The mixed material is put into the hopper of the twin-screw extruder, melted and blended, extruded and granulated to form a composite material. Among them, the temperature settings of each heating zone of the screw are as follows: first zone temperature: 185°C; second zone: 195°C; third zone: 200°C; fourth zone: 210°C; fifth zone temperature 210°C; Zone temperature 215°C; machine head: 220°C; residence time 2-3min. The pressure is 15MPa.
PUM
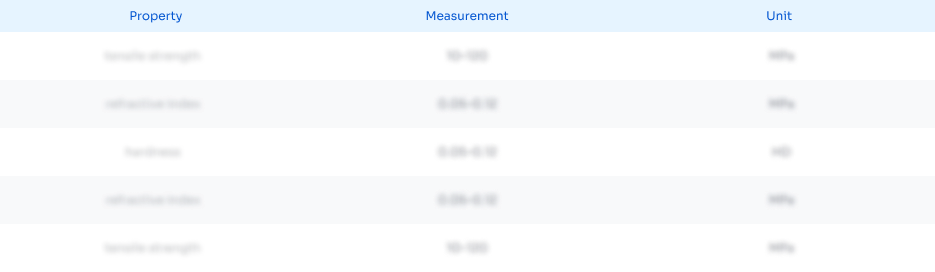
Abstract
Description
Claims
Application Information

- Generate Ideas
- Intellectual Property
- Life Sciences
- Materials
- Tech Scout
- Unparalleled Data Quality
- Higher Quality Content
- 60% Fewer Hallucinations
Browse by: Latest US Patents, China's latest patents, Technical Efficacy Thesaurus, Application Domain, Technology Topic, Popular Technical Reports.
© 2025 PatSnap. All rights reserved.Legal|Privacy policy|Modern Slavery Act Transparency Statement|Sitemap|About US| Contact US: help@patsnap.com