Manufacturing method for multilayered rigidity and flexibility combined printed circuit board
A technology of printed circuit board and manufacturing method, applied in the direction of multi-layer circuit manufacturing, etc., can solve the problems of increasing manufacturing cost, deviation of fit, and high processing cost, avoiding dislocation during processing, improving performance reliability, and qualifying products. rate increase effect
- Summary
- Abstract
- Description
- Claims
- Application Information
AI Technical Summary
Problems solved by technology
Method used
Image
Examples
Embodiment 1
[0021] Embodiment 1, the making of six-layer rigid-flexible printed wiring board, such as image 3 As shown, the specifications are two-layer flexible circuit board FPC in the middle and two-layer rigid circuit board PCB on both sides. The rigid circuit board circuit is ≥0.1mm, and the board thickness is 1.5±0.03mm. The thickness of the film is 25um, and the pure copper foil is 18um. The area is 50mm×70mm.
[0022] The specific steps are: 1. First, according to the process steps of the prior art, the flexible circuit board 7 located in the middle is completely processed;
[0023] 2. After processing the inner single-sided copper foils of the rigid circuit boards 5 and 9 on both sides of the flexible circuit board 7 according to the prior art, use a drilling machine to drill the relevant positioning holes and auxiliary holes on the side close to the flexible circuit board 7. hole;
[0024] 3. Forging machine tools are used. Forging machine tools with a tonnage of 25 tons of p...
PUM
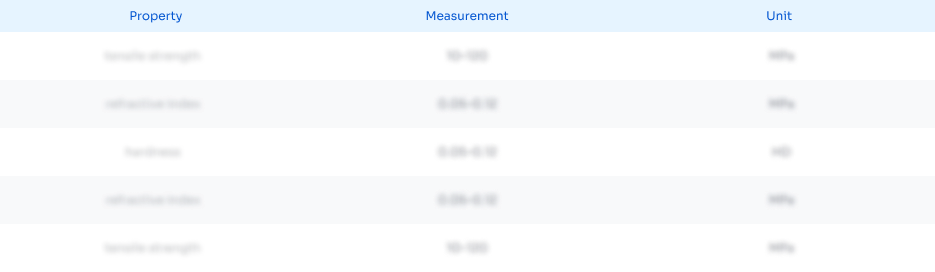
Abstract
Description
Claims
Application Information

- Generate Ideas
- Intellectual Property
- Life Sciences
- Materials
- Tech Scout
- Unparalleled Data Quality
- Higher Quality Content
- 60% Fewer Hallucinations
Browse by: Latest US Patents, China's latest patents, Technical Efficacy Thesaurus, Application Domain, Technology Topic, Popular Technical Reports.
© 2025 PatSnap. All rights reserved.Legal|Privacy policy|Modern Slavery Act Transparency Statement|Sitemap|About US| Contact US: help@patsnap.com