Method for producing limestone powder and aluminium ammonium sulfate using heat-engine plant desulfurized gypsum and fly ash
A technology for desulfurization gypsum and aluminum ammonium sulfate, which is applied in the field of producing stone powder and aluminum ammonium sulfate from desulfurization gypsum and fly ash in thermal power plants, can solve the problem of high production cost of synthetic ammonia, and achieve the advantages of saving purchase, reducing production cost and reducing emissions. Effect
- Summary
- Abstract
- Description
- Claims
- Application Information
AI Technical Summary
Problems solved by technology
Method used
Image
Examples
Embodiment 1
[0065] Raw material 1: Power plant flue gas desulfurization hydrated gypsum, CaSO 4 The content is 66.8%, the water content is 32.5%, and the rest is impurities; raw material 2: dry ash from power plants, the content of alumina is 40%, the content of iron oxide is 3.11%, the content of magnesium oxide is 0.73%, and the rest is silicon, calcium, etc.
[0066] According to the process of the present invention, 200kg of gypsum with water is processed per hour, three-stage spray absorption reaction, temperature 60°C, time 40 minutes; fly ash 75kg / h, 350°C reaction for 3 hours, clinker dissolution and leaching temperature 95°C , the leaching time was 30 minutes; the ammonium aluminum sulfate was recrystallized and purified 3 times. Limestone powder is produced at 100kg / h, aluminum ammonium sulfate 12 hydrate is produced at 350kg / h, iron hydroxide dry matter is produced at 4kg / h, and the total amount of ammonia water and liquid ammonia (calculated as NH3) is 8.2kg / h.
[0067] The i...
Embodiment 2
[0071] Raw material 1: Power plant flue gas desulfurization gypsum after natural drying, CaSO 4 The content is 74.2%, the water content is 25%, and the rest is impurities; raw material 2: dry ash from power plants, the content of alumina is 40%, the content of iron oxide is 3.11%, the content of magnesium oxide is 0.73%, and the rest is silicon, calcium, etc.
[0072] According to the process of the present invention, 1000 kg of naturally dried gypsum is processed per hour, three-stage spray absorption reaction, temperature 50 ° C, time 40 minutes; while processing fly ash 420 kg / h, 380 ° C reaction for 3 hours, clinker dissolution and leaching The temperature is 100°C, and the time is 40 minutes; ammonium aluminum sulfate is recrystallized and purified 3 times. Produce 550kg / h of stone powder, produce 2350kg / h of aluminum ammonium sulfate 12 hydrate, produce 19kg / h of ferric hydroxide dry matter, supplement the total amount of ammonia water and liquid ammonia (in NH 3 Tota...
PUM
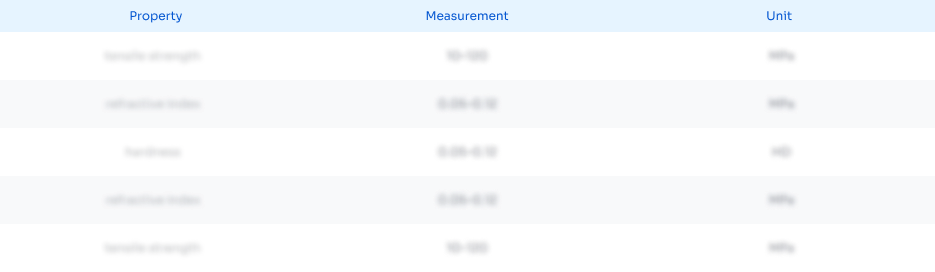
Abstract
Description
Claims
Application Information

- R&D
- Intellectual Property
- Life Sciences
- Materials
- Tech Scout
- Unparalleled Data Quality
- Higher Quality Content
- 60% Fewer Hallucinations
Browse by: Latest US Patents, China's latest patents, Technical Efficacy Thesaurus, Application Domain, Technology Topic, Popular Technical Reports.
© 2025 PatSnap. All rights reserved.Legal|Privacy policy|Modern Slavery Act Transparency Statement|Sitemap|About US| Contact US: help@patsnap.com