Cutting tool mode parameter uncertain curve five-shaft numerical control process parameter optimizing method
A modal parameter and tool technology, applied in the field of computer numerical control machining, can solve the problems of chatter vibration, can not reflect the processing status, can not achieve precision and efficient machining of parts, and achieve the effect of optimizing process parameters and improving accuracy.
- Summary
- Abstract
- Description
- Claims
- Application Information
AI Technical Summary
Problems solved by technology
Method used
Image
Examples
Embodiment Construction
[0017] The acceptance scheme of the present invention will be described in further detail below in conjunction with the drawings and examples, but the examples are not intended to limit the present invention.
[0018] The tool system modal experiment device that the embodiment of the present invention adopts is as figure 1 As shown, the carbon steel four-tooth ball-end cutter is selected as the processing tool, and the tool is clamped on the Mikron600U five-axis machine tool. The geometric parameters of the tool are: diameter 10 mm; helix angle 30 degrees; total length 100 mm; cantilever length 70 mm. According to the method of the present invention, the five-axis numerical control process parameter optimization of the curved surface with uncertain tool modal parameters is carried out, and the steps are as follows:
[0019] 1. Hit the tip of the tool with a hammer, such as figure 1 As shown, the knocking force is used as the excitation input signal, the output signal can be ...
PUM
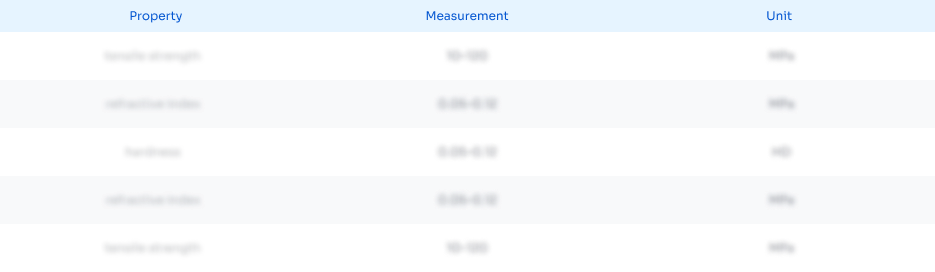
Abstract
Description
Claims
Application Information

- R&D
- Intellectual Property
- Life Sciences
- Materials
- Tech Scout
- Unparalleled Data Quality
- Higher Quality Content
- 60% Fewer Hallucinations
Browse by: Latest US Patents, China's latest patents, Technical Efficacy Thesaurus, Application Domain, Technology Topic, Popular Technical Reports.
© 2025 PatSnap. All rights reserved.Legal|Privacy policy|Modern Slavery Act Transparency Statement|Sitemap|About US| Contact US: help@patsnap.com