Process for producing saturated polychloralkane
A technology of polychlorinated alkanes and pentachloropropane, which is applied in the field of preparation of saturated polychlorinated alkanes, can solve complex problems such as processing, and achieve the effects of good reaction selectivity, complete conversion of raw materials, and high purity of products
- Summary
- Abstract
- Description
- Claims
- Application Information
AI Technical Summary
Problems solved by technology
Method used
Examples
Embodiment 1
[0023] In a glass reactor, add 1 kg of carbon trichloride, 0.8 kg of 1,1,1,3-tetrachloropropane, 1.2 kg of trichloromethanesulfonyl chloride, and 14 g of benzoyl peroxide, stir and heat to 80°C , Incubate the reaction for 8 hours. The conversion rate of the raw materials was determined by gas chromatography. The saturated aqueous solution of sodium bisulfite was added to wash twice, 0.5 kg each time, and 1 kg water was added to wash once. The organic phase was distilled to recover carbon trichloride, and the residue was distilled to obtain the product (collected at 178 degrees Distillate). The conversion rate of the raw material 1,1,1,3-tetrachloropropane was 90.4% after analysis. Based on the raw material 1,1,1,3-tetrachloropropane, the selectivity of 1,1,1,3,3-pentachloropropane is 99.0%.
Embodiment 2
[0025] Ethylene glycol dimethyl ether and trifluorotrichloroethane were used as raw materials at a molar ratio of 1:1, and the catalyst was 3.4 g cyclohexanone peroxide. The reaction was carried out using the same steps as in Example 1. After the reaction was completed, The conversion rate of the raw material 1,1,1,3-tetrachloropropane analyzed by gas chromatography was 94.6%. Based on the raw material 1,1,1,3-tetrachloropropane, the selectivity of 1,1,1,3,3-pentachloropropane was calculated to be 99.1%.
Embodiment 3
[0027] In a glass-lined reactor, add 1 kg of chlorobenzene, 0.8 kg of 1,1,1,3-tetrachloropropane, 1.2 kg of dimethylsulfuryl chloride, 0.05 kg of phosphorus pentachloride, and 12.2 of azobisisoheptonitrile. G, stir and react at 0-40°C for 12 hours. The conversion rate of the raw materials was determined by gas chromatography. The saturated potassium thiosulfate aqueous solution was added to wash twice, 0.5 kg each time, and 1 kg water was added to wash once. The organic phase was distilled to recover chlorobenzene, and the residue was distilled to obtain the product. The conversion rate of the raw material 1,1,1,3-tetrachloropropane was 75% after analysis. Based on the raw material 1,1,1,3-tetrachloropropane, the selectivity to 1,1,1,3,3-pentachloropropane is 99.0%.
PUM
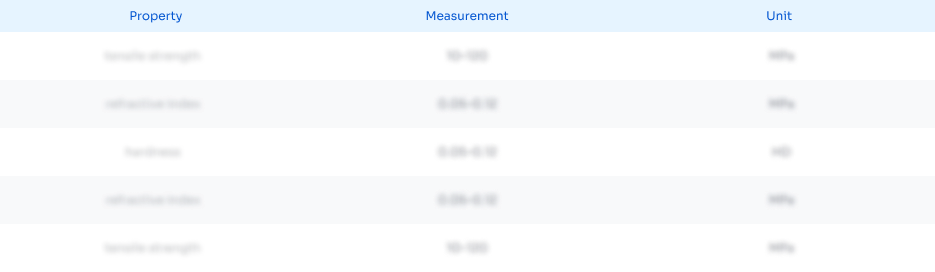
Abstract
Description
Claims
Application Information

- R&D
- Intellectual Property
- Life Sciences
- Materials
- Tech Scout
- Unparalleled Data Quality
- Higher Quality Content
- 60% Fewer Hallucinations
Browse by: Latest US Patents, China's latest patents, Technical Efficacy Thesaurus, Application Domain, Technology Topic, Popular Technical Reports.
© 2025 PatSnap. All rights reserved.Legal|Privacy policy|Modern Slavery Act Transparency Statement|Sitemap|About US| Contact US: help@patsnap.com