Wax shale gray slag base polymer gelled material
A technology of oil shale ash and polymer glue, which is applied in the field of light building materials, can solve problems such as adverse effects on the surrounding environment, environmental pollution, waste of resources, etc., and achieve low production prices, huge economic and social benefits, and a wide range of applications Effect
- Summary
- Abstract
- Description
- Claims
- Application Information
AI Technical Summary
Problems solved by technology
Method used
Image
Examples
Embodiment 1
[0028] Blend 37% oil shale ash with 31% calcined kaolin, 17% cement, 5% quicklime, and 4% industrial alkali. After mixing evenly, add 8% activator, and add 5 to 25 %, mixed and stirred for 2 minutes to obtain a composite slurry. The composite molding material is gray after solidification, can be colored, has a hard texture and good plasticity.
Embodiment 2
[0030] Blend 47% oil shale ash with 21% calcined kaolin, 15% cement, 4% quicklime, and 3% industrial alkali. After mixing evenly, add 8% activator, and add 5 to 25 %, mixed and stirred for 2 minutes to obtain a composite slurry. The composite molding material is gray after solidification, can be colored, has a hard texture and good plasticity.
Embodiment 3
[0032] Blend the oil shale ash with a weight ratio of 58% with 10% calcined kaolin, 17% cement, 4% quicklime, and 4% industrial alkali. %, mixed and stirred for 2 minutes to obtain a composite slurry. The composite modeling material is dark gray after solidification, can be colored, has a hard texture and good plasticity.
PUM
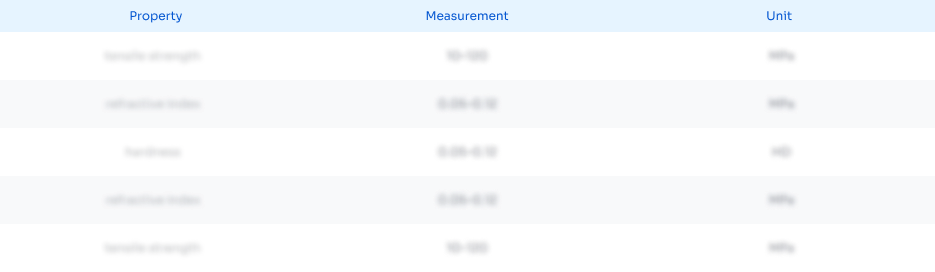
Abstract
Description
Claims
Application Information

- Generate Ideas
- Intellectual Property
- Life Sciences
- Materials
- Tech Scout
- Unparalleled Data Quality
- Higher Quality Content
- 60% Fewer Hallucinations
Browse by: Latest US Patents, China's latest patents, Technical Efficacy Thesaurus, Application Domain, Technology Topic, Popular Technical Reports.
© 2025 PatSnap. All rights reserved.Legal|Privacy policy|Modern Slavery Act Transparency Statement|Sitemap|About US| Contact US: help@patsnap.com