Foam flotation method capable of separating silicon powder and carbon silicon powder
A silicon carbide powder and foam flotation technology, which is applied in flotation, solid separation, grinding/polishing equipment, etc., can solve the problems of few patents, toxicity, and difficulty in liquid phase gravity flotation, and achieve good results. The effect of easy demarcation
- Summary
- Abstract
- Description
- Claims
- Application Information
AI Technical Summary
Problems solved by technology
Method used
Examples
Embodiment 1
[0016] The foam flotation method for separating silicon powder and silicon carbide powder, adding a treatment agent to the mortar produced by the silicon wafer wire sawing process, the ratio by weight is 100-1000 parts of mortar: 100-1000 parts of treatment agent; Stir evenly with the treatment agent, the sedimentation is divided into three layers, and the upper layer of silicon carbide and the lower layer of silicon powder are collected respectively; the middle is the liquid layer;
[0017] The treatment agent comprises a solvent and a surface modifying agent mixed in proportion, and the mixing ratio is 99-70% by weight of the solvent and 1-30% of the surface modifying agent; wherein the solvent is ethanol, methanol, water, diesel oil and kerosene at least one or several, and the surface modifier is at least one or several of alkylphenol polyoxyethylene ether, octylphenol polyoxyethylene ether, oleic acid, and terpineol.
[0018] Scrape the upper layer of silicon carbide floa...
Embodiment 2
[0020] The foam flotation method for separating silicon powder and silicon carbide powder, adding a treatment agent to the mortar produced by the silicon wafer wire saw process, the ratio by weight is 100 parts of mortar: 1000 parts of treatment agent; the mortar and treatment agent are stirred Uniform, natural sedimentation is divided into three layers, the upper layer of silicon carbide and the lower layer of silicon powder are collected respectively; the middle is the liquid layer;
[0021] The treatment agent comprises a solvent and a surface modifying agent mixed in proportion, the mixing ratio is 80% by weight of the solvent, 20% of the surface modifying agent; wherein the solvent is 40% of ethanol and 40% of water, and the surface modifying agent It is 10% of alkylphenol polyoxyethylene ether and 10% of octylphenol polyoxyethylene ether.
[0022] Scrape the upper layer of silicon carbide floating matter from the surface; collect the silicon powder sediment from the lowe...
Embodiment 3
[0024] The foam flotation method for separating silicon powder and silicon carbide powder, adding a treatment agent to the mortar produced by the silicon wafer wire saw process, the ratio by weight is 100 parts of mortar: 1000 parts of treatment agent; the mortar and treatment agent are stirred Uniform, natural sedimentation is divided into three layers, the upper layer of silicon carbide and the lower layer of silicon powder are collected respectively; the middle is the liquid layer;
[0025] The treatment agent comprises a solvent and a surface modifier mixed in proportion, and the mixing ratio is 60% by weight of ethanol, a solvent composed of 20% of water, 15% of alkylphenol polyoxyethylene ether, and 5% of octylphenol Surface modifier composed of polyoxyethylene ether. Scrape the upper layer of silicon carbide floating matter from the surface; collect the silicon powder sediment from the lower layer.
PUM
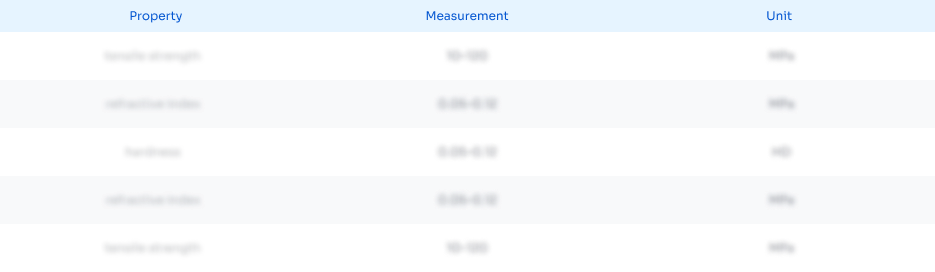
Abstract
Description
Claims
Application Information

- R&D Engineer
- R&D Manager
- IP Professional
- Industry Leading Data Capabilities
- Powerful AI technology
- Patent DNA Extraction
Browse by: Latest US Patents, China's latest patents, Technical Efficacy Thesaurus, Application Domain, Technology Topic, Popular Technical Reports.
© 2024 PatSnap. All rights reserved.Legal|Privacy policy|Modern Slavery Act Transparency Statement|Sitemap|About US| Contact US: help@patsnap.com