Two-step plasticity forming method of vehicle wheel hub and mated forming die
An automobile wheel hub, plastic forming technology, applied in the direction of wheels, metal extrusion dies, vehicle parts, etc., can solve the problems of increased production cost, unfavorable promotion and development, difficulty in rim forming, etc., to reduce production costs, improve mechanical properties, The effect of reducing equipment and mold investment
- Summary
- Abstract
- Description
- Claims
- Application Information
AI Technical Summary
Problems solved by technology
Method used
Image
Examples
Embodiment Construction
[0032] Such as figure 1 as shown, figure 1 Middle picture a) is the billet making process, picture b) is the extrusion process, and picture c) is the flaring process. In the figure, according to the viewing position during its use, the wheel rim part above the spoke is called the front wheel rim, and the wheel rim part below the wheel spoke is called the rear wheel rim. The technological process of the forming method of the automobile wheel hub is as follows: billet making——extruding the spoke part and preforming the front and rear rims of the rim——expanding the preformed parts to form the front and rear rims of the rim. Its main steps are as follows:
[0033] 1. The wheel hub material is made of aging cast or rolled magnesium alloy rods, such as AZ31B, AZ61, AZ91D, AZ80A, etc., and is cut into billets by sawing according to the required size.
[0034] 2. Heat each mold according to the process requirements. In order to realize isothermal extrusion forming, the heating temp...
PUM
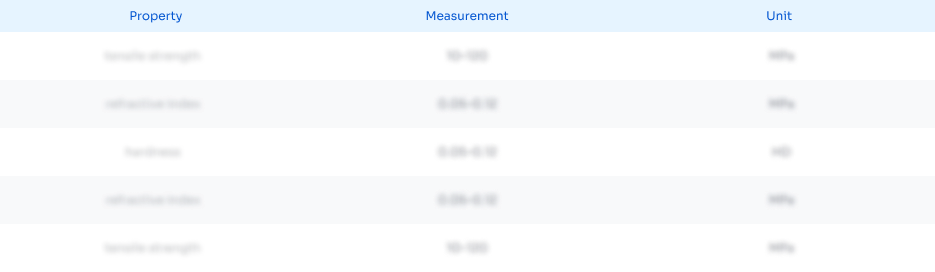
Abstract
Description
Claims
Application Information

- R&D
- Intellectual Property
- Life Sciences
- Materials
- Tech Scout
- Unparalleled Data Quality
- Higher Quality Content
- 60% Fewer Hallucinations
Browse by: Latest US Patents, China's latest patents, Technical Efficacy Thesaurus, Application Domain, Technology Topic, Popular Technical Reports.
© 2025 PatSnap. All rights reserved.Legal|Privacy policy|Modern Slavery Act Transparency Statement|Sitemap|About US| Contact US: help@patsnap.com