High saturation magnetic flux density low loss soft magnetic ferrite material and producing method thereof
A soft ferrite and magnetic flux density technology, applied in the direction of inorganic material magnetism, etc., can solve the problems of high saturation magnetic flux density, low cost and large loss, and achieve high saturation magnetic flux density, low cost and low loss. Effect
- Summary
- Abstract
- Description
- Claims
- Application Information
AI Technical Summary
Problems solved by technology
Method used
Image
Examples
Embodiment 1
[0033] with Fe 2 o 3 54.6mol%, MnO 43.4mol%, ZnO 2mol% weigh Fe as the main formula content 2 o 3 , MnO, and ZnO raw materials were wet-mixed, and then pre-fired at 900°C for 2 hours. According to the weight of the main formula, to the pre-fired mixture relative to Fe 2 o 3 The total amount of , MnO, ZnO is calculated by adding 150ppm of SiO in weight percentage 2 , 900ppm of CaCO 3 , 200ppm ZrO 2 , 200ppm Nb 2 o 5 and 100ppm Na 2 O, where Na 2 O with NaCl or Na 2 CO 3 The form of adding, wet sanding, ferrite slurry. Add 1wt% PVA binder calculated by ferrite powder weight to the slurry for spray granulation. Under a certain pressure, the granulated powder is molded into a standard ring ferrite core for testing. The molded body was sintered at 1250° C. for 0.5 hour under the condition of oxygen partial pressure concentration of 0.1%, wherein the heating rate was 4° C. / min during the heating stage of 1000° C. to 1250° C., and the oxygen partial pressure concentra...
Embodiment 2
[0036] with Fe 2 o 3 54.5mol%, MnO 42.5mol%, ZnO 3mol% weigh Fe as the main formula content 2 o 3, MnO, and ZnO raw materials were wet-mixed, and then pre-fired at 900°C for 2 hours. According to the weight of the main formula, add 150ppm of SiO to the pre-fired mixture in terms of weight percentage relative to the total amount of Fe2O3, MnO, and ZnO 2 , 900ppm of CaCO 3 , 200ppm ZrO 2 , 200ppm Nb 2 o 5 and 100ppm Na 2 O, where Na 2 O with NaCl or Na 2 CO 3 The form of adding, wet sanding, ferrite slurry. Add 1wt% PVA binder calculated by ferrite powder weight to the slurry for spray granulation. Under a certain pressure, the granulated powder is molded into a standard ring ferrite core for testing. The molded body was sintered at 1250° C. for 1 hour under the condition of oxygen partial pressure concentration of 0.01%, wherein the heating rate was 4° C. / min in the heating stage of 1000° C. to 1250° C., and the oxygen partial pressure concentration was 1%. Cooli...
Embodiment 3
[0039] with Fe 2 o 3 54.3mol%, MnO 41.7mol%, ZnO 4mol% weigh Fe as the main formula content 2 o 3 , MnO, and ZnO raw materials were wet-mixed, and then pre-fired at 900°C for 2 hours. According to the weight of the main formula, add 150ppm of SiO to the pre-fired mixture in terms of weight percentage relative to the total amount of Fe2O3, MnO, and ZnO 2 , 900ppm of CaCO 3 , 200ppm ZrO 2 , 200ppm Nb 2 o 5 and 100ppm Na 2 O, where Na 2 O with NaCl or Na 2 CO 3 The form of adding, wet sanding, ferrite slurry. Add 1wt% PVA binder calculated by ferrite powder weight to the slurry for spray granulation. Under a certain pressure, the granulated powder is molded into a standard ring ferrite core for testing. The molded body was sintered at 1250° C. for 3 hours under the condition of oxygen partial pressure concentration of 0.005%, wherein the heating rate was 4° C. / min in the heating stage of 1000° C. to 1250° C., and the oxygen partial pressure concentration was 3%. Co...
PUM
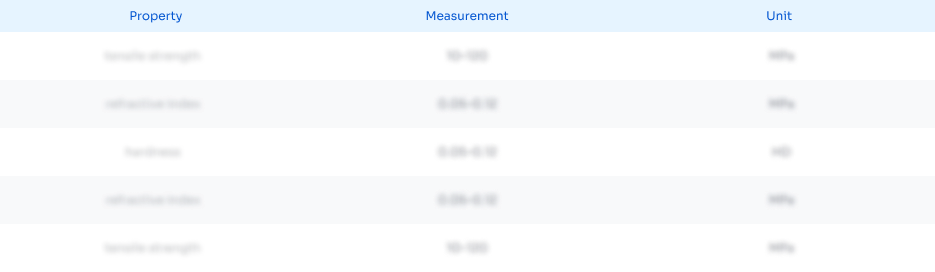
Abstract
Description
Claims
Application Information

- R&D
- Intellectual Property
- Life Sciences
- Materials
- Tech Scout
- Unparalleled Data Quality
- Higher Quality Content
- 60% Fewer Hallucinations
Browse by: Latest US Patents, China's latest patents, Technical Efficacy Thesaurus, Application Domain, Technology Topic, Popular Technical Reports.
© 2025 PatSnap. All rights reserved.Legal|Privacy policy|Modern Slavery Act Transparency Statement|Sitemap|About US| Contact US: help@patsnap.com