Butt joint method of thin-wall metal pipe
A technology for metal thin-walled pipes, which is applied in the direction of pipes/pipe joints/fittings, sockets/socket connections, passing components, etc., which can solve the problem of no adjustment allowance for metal thin-walled pipes, shortened service life of pipe fittings, and insufficient tensile strength and other problems, to achieve the effects of strong impact resistance, material saving, and improved oxidation resistance
- Summary
- Abstract
- Description
- Claims
- Application Information
AI Technical Summary
Problems solved by technology
Method used
Image
Examples
Embodiment
[0012] Embodiment (adopting an automobile smoke exhaust pipe that the method of the present invention is butted):
[0013] Such as Figure 4 The automobile smoke exhaust pipe shown is composed of parts one 1, metal thin-walled elbow one 2, metal thin-walled straight pipe two 3, metal thin-walled elbow three 4, metal thin-walled straight pipe four 5, metal thin-walled straight pipe five 6 , part two 7, hoop 8, bolt 9, nut 10, adopt the method of the present invention butt joint with bolt 9, nut 10, hoop 8, metal thin-walled elbow one 2, metal thin-walled straight pipe two 3, Metal thin-walled curved pipe three 4, metal thin-walled straight pipe four 5, metal thin-walled straight pipe five 6 are connected and fastened together, and then installed on part one 1 and part two 7. Since every two metal thin-walled tubes can be rotated 360°, the steel tube has a relatively large amount of adjustment, which can overcome the existing metal tubes that are prone to breakage, disjoint, an...
PUM
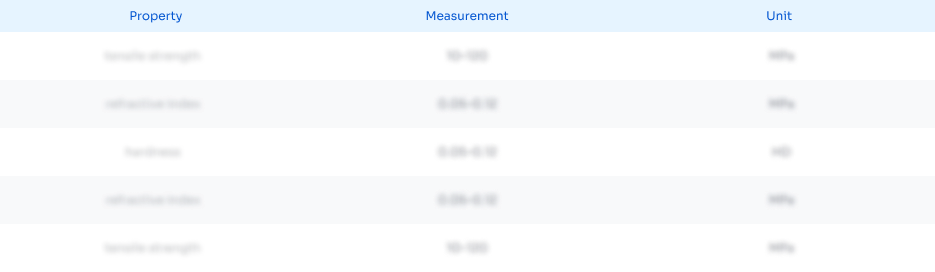
Abstract
Description
Claims
Application Information

- R&D
- Intellectual Property
- Life Sciences
- Materials
- Tech Scout
- Unparalleled Data Quality
- Higher Quality Content
- 60% Fewer Hallucinations
Browse by: Latest US Patents, China's latest patents, Technical Efficacy Thesaurus, Application Domain, Technology Topic, Popular Technical Reports.
© 2025 PatSnap. All rights reserved.Legal|Privacy policy|Modern Slavery Act Transparency Statement|Sitemap|About US| Contact US: help@patsnap.com