Coupling fixed bed oxygen-enriched continuous gasification process
A fixed-bed, coupled technology, applied in the petroleum industry, combined combustion mitigation, manufacturing of combustible gas, etc., can solve the problems of sensible heat loss, low utilization rate of raw materials, high blowing intensity, etc. Heat loss, effect of improving air condition
- Summary
- Abstract
- Description
- Claims
- Application Information
AI Technical Summary
Problems solved by technology
Method used
Image
Examples
Embodiment Construction
[0062] The first embodiment of the present invention, such as figure 1 As shown in the coupled fixed bed oxygen-enriched continuous gasification process, the solid raw material is coal, and the process is to mix oxygen and air to form oxygen-enriched air, then blow in oxygen-enriched air and steam to produce semi-water gas; the gas-making furnace includes a 1, B, two ordinary gas furnaces, the bottom of A furnace is connected with oxygen-enriched air valve A1, steam valve A3, gas valve A5, and the bottom of B furnace is connected with oxygen-enriched air valve B2, steam valve B4, and gas valve B 6; the gas outlets on the top of furnace A and furnace B are connected in parallel with gas valve C 7, and the other end of gas valve C 7 is connected with the other end of gas valve A 5 and gas valve B 6 through a four-way joint. The other end is connected to the output pipe.
[0063] The cycle time of the gas generation process is 120 seconds, the oxygen concentration in the oxygen-...
PUM
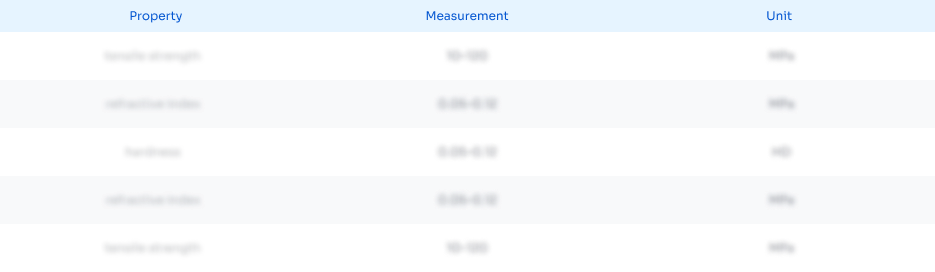
Abstract
Description
Claims
Application Information

- R&D
- Intellectual Property
- Life Sciences
- Materials
- Tech Scout
- Unparalleled Data Quality
- Higher Quality Content
- 60% Fewer Hallucinations
Browse by: Latest US Patents, China's latest patents, Technical Efficacy Thesaurus, Application Domain, Technology Topic, Popular Technical Reports.
© 2025 PatSnap. All rights reserved.Legal|Privacy policy|Modern Slavery Act Transparency Statement|Sitemap|About US| Contact US: help@patsnap.com