Technological process for producing cement clinker by dry burning carbide slag
A technology of cement clinker and process method, which is applied in the direction of cement production, etc., which can solve the problems of low thermal efficiency, serious system return, affecting the stable calcination of rotary kiln, etc., and achieve the effect of high thermal efficiency and stable system operation
- Summary
- Abstract
- Description
- Claims
- Application Information
AI Technical Summary
Problems solved by technology
Method used
Image
Examples
Embodiment Construction
[0013] Referring to the accompanying drawings, the mixture of calcium carbide slag and auxiliary materials after drying and grinding is used as the raw meal, which is heated and decomposed step by step by the five-stage cyclone, and the raw meal first enters the ascending pipe at the upper part of the second-stage cyclone 2 The first heat exchange occurs when the inside and the hot air flow meet and merge, and enter the primary cyclone 1 for the first separation of gas and material. The ascending pipe entering the upper part of the third-stage cyclone 3 meets the hot air flow for the second heat exchange and enters the second-stage cyclone 2 for the second gas-material separation. The feeding pipe at the bottom of the cyclone 2 then enters the ascending pipe at the top of the fourth-stage cyclone 4, meets and merges with the hot air flow for the third heat exchange and enters the third-stage cyclone 3 for the third gas-material separation, and the third gas-material separation....
PUM
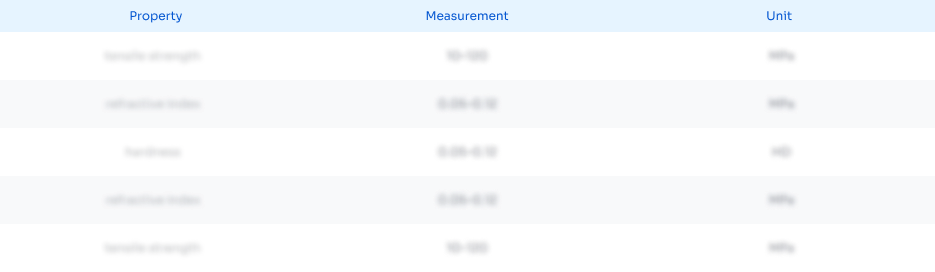
Abstract
Description
Claims
Application Information

- Generate Ideas
- Intellectual Property
- Life Sciences
- Materials
- Tech Scout
- Unparalleled Data Quality
- Higher Quality Content
- 60% Fewer Hallucinations
Browse by: Latest US Patents, China's latest patents, Technical Efficacy Thesaurus, Application Domain, Technology Topic, Popular Technical Reports.
© 2025 PatSnap. All rights reserved.Legal|Privacy policy|Modern Slavery Act Transparency Statement|Sitemap|About US| Contact US: help@patsnap.com