Selective non-catalytic reduction method with added gasified biomass gas and used boiler
A technology of biomass and gasification gas, applied in chemical instruments and methods, separation methods, lighting and heating equipment, etc., can solve the problems of low denitrification rate, narrow temperature window, single active ingredient, etc., and achieve simple boiler system, high temperature The effect of wide window and wide distribution
- Summary
- Abstract
- Description
- Claims
- Application Information
AI Technical Summary
Problems solved by technology
Method used
Image
Examples
specific Embodiment approach 1
[0010] Specific implementation mode one: combine figure 1 Describe this embodiment, this embodiment includes a body, a burner 4, a panel superheater 7, a high and low temperature superheater 8, a reheater 10, two economizers 12 and two air preheaters 13, the body It is made of a furnace 5, a horizontal flue 9 and a tail flue 11. The outer wall of the furnace 5 is equipped with a burner 4, the panel superheater 7, a high and low temperature superheater 8 and a reheater 10 along the flue The flow direction of the gas in the horizontal flue 9 is installed in the horizontal flue 9 in sequence, and the two economizers 12 and the two air preheaters 13 are arranged at the tail at intervals along the flow direction of the flue gas in the tail flue 11 In the flue 11, the boiler also includes an amino reducing agent solution pipeline 1, a compressed air pipeline 2, a plurality of spray guns 3, a biomass gasification device 14, a pressurizing device 15, a plurality of gas additive injecti...
specific Embodiment approach 2
[0011] Specific implementation mode two: combination figure 1 Describe this embodiment, the selective non-catalytic reduction method of adding biomass gasification gas in this embodiment is as follows: fill the amino reducing agent solution into the amino reducing agent solution pipeline 1, spray the amino reducing agent solution through a plurality of spray guns 3 Into the furnace 5 and the horizontal flue 9 near the refraction angle 6, the temperature range in the furnace 5 and the horizontal flue 9 near the refraction angle is 900 ° C ~ 1100 ° C, and the injection of the amino reducing agent solution is always Amount of NH produced by reducing agent 3 Expressed by the molar ratio of NOx in the flue gas before the reducing agent is injected, NH 3 The molar ratio to NOx in the flue gas is 1.1-1.8; and the amount of the ammonia reductant solution injected into the furnace before the biomass gasification gas is injected is based on the NH produced by the reductant 3 Expresse...
specific Embodiment approach 3
[0012] Specific embodiment three: the difference between this embodiment and specific embodiment two is: the total amount of the injection of the amino reducing agent solution is based on the NH produced by the reducing agent 3 The molar ratio of NOx in the flue gas before the amino reducing agent solution is sprayed is 1.5-1.8. The denitrification efficiency reaches 40-65%.
PUM
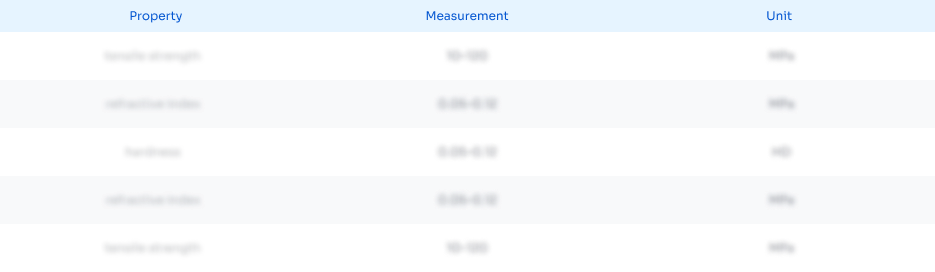
Abstract
Description
Claims
Application Information

- R&D
- Intellectual Property
- Life Sciences
- Materials
- Tech Scout
- Unparalleled Data Quality
- Higher Quality Content
- 60% Fewer Hallucinations
Browse by: Latest US Patents, China's latest patents, Technical Efficacy Thesaurus, Application Domain, Technology Topic, Popular Technical Reports.
© 2025 PatSnap. All rights reserved.Legal|Privacy policy|Modern Slavery Act Transparency Statement|Sitemap|About US| Contact US: help@patsnap.com