Composite steel pipe with plastic tape winded externally and plastic coated internally, and its processing method
A technology of composite steel pipe and processing method, which is applied in the direction of coating, pipe, rigid pipe, etc., can solve the problems of waste products, high processing cost, and difficult to solve pipe wear resistance and impact resistance, so as to reduce production cost, production efficiency and Comprehensive performance improvement, easy spraying effect
- Summary
- Abstract
- Description
- Claims
- Application Information
AI Technical Summary
Problems solved by technology
Method used
Image
Examples
Embodiment Construction
[0027] figure 1 Shown is the composite steel pipe structure of the present invention whose outer wall is wound with a plastic tape and whose inner wall is sprayed with plastic. The main innovation of the present invention is to use the existing plastic tape extrusion equipment and winding equipment to wind the polyethylene plastic tape 2 on the rotating steel pipe 1, Spray polyurea plastic coating layer 3 in the steel pipe, the present invention's winding plastic tape and the equipment schematic diagram of spraying plastic coating layer shown in Fig. 2, processing process is as follows:
[0028] A. The steel pipe is placed on the roller bracket 4 to rotate, and the inner and outer walls are cleaned to a level 2 cleaning level by sandblasting;
[0029] B. The steel pipe is placed on the roller bracket 4 to rotate and preheated to 160-180°C;
[0030] C. The steel pipe is placed on the roller bracket 4 to rotate, and a layer of 3-5mm polyethylene plastic tape winding layer 2 is ...
PUM
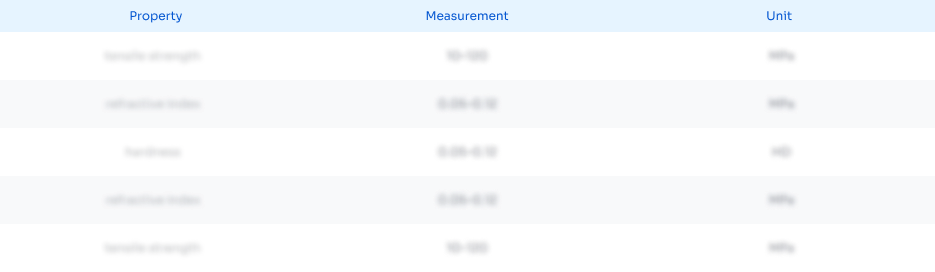
Abstract
Description
Claims
Application Information

- Generate Ideas
- Intellectual Property
- Life Sciences
- Materials
- Tech Scout
- Unparalleled Data Quality
- Higher Quality Content
- 60% Fewer Hallucinations
Browse by: Latest US Patents, China's latest patents, Technical Efficacy Thesaurus, Application Domain, Technology Topic, Popular Technical Reports.
© 2025 PatSnap. All rights reserved.Legal|Privacy policy|Modern Slavery Act Transparency Statement|Sitemap|About US| Contact US: help@patsnap.com