Process for manufacturing pipeline tube
A process method and line pipe technology are applied in the processing field of the production line pipe of seamless oil well steel pipe restraint continuous rolling unit, which can solve the problems of many steel pipe transportation processes, high production cost, low production rhythm, etc., and achieve surface scratches, etc. Reduced chance of defects in quality, reduced transportation process, improved production rhythm effect
- Summary
- Abstract
- Description
- Claims
- Application Information
AI Technical Summary
Problems solved by technology
Method used
Examples
Embodiment 1
[0014] Example 1: Put the tube billet into a ring heating furnace for heating, preheat at 1030°C for 10 minutes, preheat at 1200°C for 15 minutes, heat at 1320°C for 20 minutes, and heat at 1310°C for 25 minutes. Soak at 1290°C for 25 minutes, and at a furnace temperature of 1280°C for 20 minutes. After being released from the furnace, the tube billet temperature is 1300°C. The tube billet after being released from the furnace is rolled into a piercing machine. Left and right; the perforated capillary is sprayed with borax antioxidant and reaches the mandrel for pre-threading. After the capillary is pre-threaded through the mandrel, the capillary is turned by the rotary arm to the rolling line of the continuous rolling mill for rolling. , The action cycle of the slewing arm is 26.28 seconds. After being rolled by the stripping machine, the blank tube is separated from the mandrel, and the blank tube goes to the next process to ensure that the temperature of the blank tube leavi...
Embodiment 2
[0015] Example 2: put the tube billet into a ring heating furnace for heating, preheat at 1120°C for 10 minutes, preheat at 1270°C for 15 minutes, heat at 1310°C for 20 minutes, and heat at 1315°C for 25 minutes. Soak at 1300°C for 25 minutes, and at a furnace temperature of 1290°C for 20 minutes. After being released from the furnace, the tube billet temperature is 1300°C. The tube billet after being released from the furnace enters the piercing machine for rolling, and the solid tube billet becomes a capillary tube after being pierced. Left and right; the perforated capillary is sprayed with borax antioxidant and reaches the mandrel for pre-threading. After the capillary is pre-threaded through the mandrel, the capillary is turned by the rotary arm to the rolling line of the continuous rolling mill for rolling. , The action cycle of the slewing arm is 26.28 seconds. After being rolled by the stripping machine, the blank tube is separated from the mandrel, and the blank tube g...
Embodiment 3
[0016] Example 3: put the tube billet into a ring heating furnace for heating, preheat at a furnace temperature of 1080°C for 10 minutes, preheat at a furnace temperature of 1240°C for 15 minutes, heat at a furnace temperature of 1310°C for 20 minutes, and heat at a furnace temperature of 1320°C for 25 minutes. Soak at 1280°C for 25 minutes, and at a furnace temperature of 1300°C for 20 minutes. After being released from the furnace, the temperature of the tube blank is 1300°C. The tube blank that comes out of the furnace enters the piercing machine for rolling, and the solid tube blank becomes a capillary tube after being pierced. The temperature at this time is 1200°C Left and right; the perforated capillary is sprayed with borax antioxidant and reaches the mandrel for pre-threading. After the capillary is pre-threaded through the mandrel, the capillary is turned by the rotary arm to the rolling line of the continuous rolling mill for rolling. , The action cycle of the slewin...
PUM
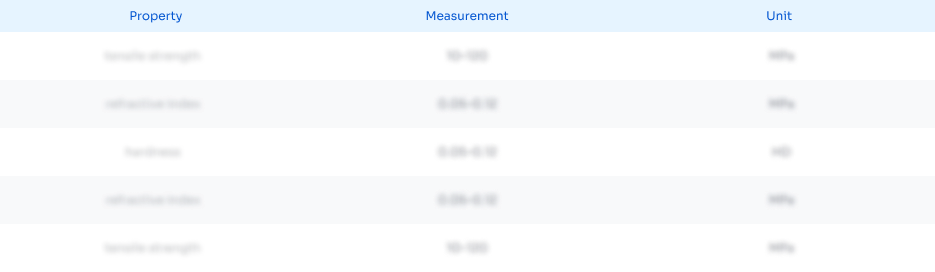
Abstract
Description
Claims
Application Information

- Generate Ideas
- Intellectual Property
- Life Sciences
- Materials
- Tech Scout
- Unparalleled Data Quality
- Higher Quality Content
- 60% Fewer Hallucinations
Browse by: Latest US Patents, China's latest patents, Technical Efficacy Thesaurus, Application Domain, Technology Topic, Popular Technical Reports.
© 2025 PatSnap. All rights reserved.Legal|Privacy policy|Modern Slavery Act Transparency Statement|Sitemap|About US| Contact US: help@patsnap.com