Ceramic powder, and method for production of ceramic powder
A technology of ceramic powder and manufacturing method, which is applied in the manufacture/assembly of piezoelectric/electrostrictive devices, chemical instruments and methods, niobium compounds, etc., can solve the problems of increased manufacturing cost, composition deviation, easy evaporation of alkali metals, etc. , to achieve the effects of easy preservation and management, improving synthesis, and reducing manufacturing costs
- Summary
- Abstract
- Description
- Claims
- Application Information
AI Technical Summary
Problems solved by technology
Method used
Image
Examples
Embodiment 1
[0087] As a ceramic raw material, K is prepared 2 CO 3 , Nb 2 O 5 , Yb 2 O 3 , Y 2 O 3 , In 2 O 3 , Nd 2 O 3 , Eu 2 O 3 , Gd 2 O 3 , Dy 2 O 3 , Sm 2 O 3 , Ho 2 O 3 , Er 2 O 3 , Tb 2 O 3 , Lu 2 O 3 , La 2 O 3 And Bi 2 O 3 .
[0088] Then, according to the general formula: KNbO 3 +xM1O 3 / 2 In, to achieve the composition shown in Table 3, these ceramic raw materials were weighed.
[0089] After that, these weighed objects were put into a ball mill together with ethanol and PSZ, and the ethanol was wet-mixed. After the obtained mixture was dried, it was fired at a temperature of 900° C. for 2 hours to prepare each sample (ceramic powder) with sample numbers 1 to 20.
[0090] Then, using an X-ray diffractometer and CuK α rays as the X-ray source, the X-ray diffraction spectrum of each sample was measured shortly after firing, and the maximum peak intensity I of the different phase was calculated. D With KNbO 3 The maximum peak intensity I KN The intensity ratio of X, evaluates the degr...
Embodiment 2
[0107] In addition to the ceramic material of [Example 1], Na is also prepared 2 CO 3 , Using the same method and procedure as [Example 1], the general formula {(K 1-α Na α )NbO 3 +x M1O 3 / 2 } (Wherein α is 0.5 or 0.9) represents each sample (ceramic powder) of sample numbers 21 to 42.
[0108] Then, for each of the samples of sample numbers 21 to 42, the strength ratio X, the pH immediately after firing and 1000 hours after firing were measured by the same method and procedure as in [Example 1].
[0109] Table 4 shows the composition and measurement results of each sample with sample numbers 21 to 42.
[0110] [Table 4]
[0111]
[0112] * Indicates outside the scope of the present invention
[0113] Sample Nos. 21 to 32 contain the specific element M1 within the scope of the present invention. Therefore, it is the same as the sample Nos. 1 to 12 in [Example 1]. Soon after or after 1000 hours of calcination, the result was 7, showing neutrality, indicating that it was not deliq...
Embodiment 3
[0122] As a ceramic raw material, K is prepared 2 CO 3 , Na 2 CO 3 , Nb 2 O 5 , Yb 2 O 3 , TiO 2 , ZrO 2 And SnO 2 .
[0123] Then, follow the general formula: ANbO 3 +0.02YbO 3 / 2 +0.04M2O 2 In, the ceramic raw materials were weighed to achieve the composition shown in Table 5.
[0124] Thereafter, each sample (ceramic powder) with sample numbers 51 to 56 was produced by the same method and procedure as in [Example 1].
[0125] Then, for each of the samples with sample numbers 51 to 56, the strength ratio X and the pH immediately after firing and 1000 hours after firing were measured by the same method and procedure as in [Example 1].
[0126] Table 5 shows the composition and measurement results of each sample with sample numbers 51-56.
[0127] [table 5]
[0128]
[0129] It can be clearly seen from Table 5 that even when tetravalent Ti, Zr, and Sn are added to the composition of sample number 1 or sample number 21 as element M2, the intensity ratio is 0%. Out of phase. In add...
PUM
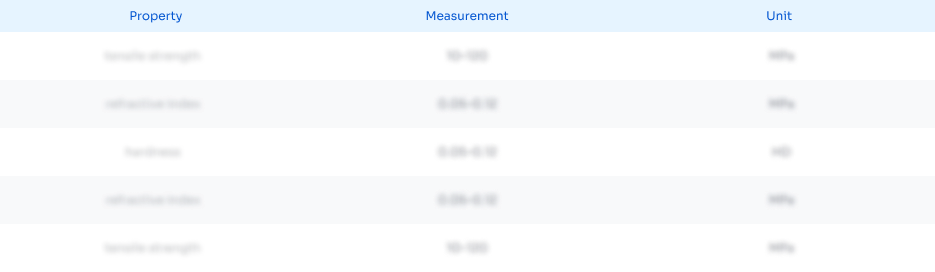
Abstract
Description
Claims
Application Information

- R&D
- Intellectual Property
- Life Sciences
- Materials
- Tech Scout
- Unparalleled Data Quality
- Higher Quality Content
- 60% Fewer Hallucinations
Browse by: Latest US Patents, China's latest patents, Technical Efficacy Thesaurus, Application Domain, Technology Topic, Popular Technical Reports.
© 2025 PatSnap. All rights reserved.Legal|Privacy policy|Modern Slavery Act Transparency Statement|Sitemap|About US| Contact US: help@patsnap.com