Electronic emitter and production method thereof, electron source and visual display unit
一种电子发射、制造方法的技术,应用在图像/图形显示管、电极系统制造、放电管/灯的制造等方向,能够解决电子漫射、表面粗糙度大、制造出电子发射器件等问题,达到性能卓越的效果
- Summary
- Abstract
- Description
- Claims
- Application Information
AI Technical Summary
Problems solved by technology
Method used
Image
Examples
no. 1 example
[0085] In the following, reference will be made to figure 1 The steps of manufacturing the electron emission film according to this example are described in detail.
[0086] (step 1)
[0087] First, quartz glass as the substrate 101 was sufficiently cleaned, and a Pt film as the cathode electrode 102 was formed on the substrate 101 with a thickness of 200 nm by the sputtering method.
[0088] (step 2)
[0089] A diamond-like carbon film containing Pt was formed as the electron emission film 103 on the cathode electrode 102 by using a co-sputtering method. The film thickness was about 30 nm, and the Pt density was about 20%.
[0090] (step 3)
[0091] The surface termination treatment was performed under the following conditions to form the hydrogen terminated surface 104 .
[0092] Process gas: CH 4 50 sccm
[0093] Pressure: 0.25Pa
[0094] ECR plasma power: 300W
[0095] Grid bias: -80V
[0096] Substrate Bias: +40V
[0097] Processing time: 30 seconds
[0098] ...
no. 2 example
[0101] In the following, reference will be made to figure 1 The steps of manufacturing the electron emission film according to this example are described in detail.
[0102] (step 1)
[0103] First, quartz glass as the substrate 101 was sufficiently cleaned, and a Pt film as the cathode electrode 102 was formed on the substrate 101 with a thickness of 200 nm by the sputtering method.
[0104] (step 2)
[0105] A Co-containing diamond-like carbon film was formed as the electron emission film 103 on the cathode electrode 102 by using a co-sputtering method. The film thickness was about 30 nm, and the Co density was about 20%.
[0106] (step 3)
[0107] The surface termination treatment was performed under the following conditions to form the hydrogen terminated surface 104 .
[0108] Process gas: CH 4 20 sccm
[0109] h 2 30 sccm
[0110] Pressure: 0.25Pa
[0111] ECR plasma power: 400W
[0112] Grid bias: 0V
[0113] Substrate Bias: +40V
[0114] Processing time:...
no. 3 example
[0118] In the following, reference will be made to figure 1 The steps of manufacturing the electron emission film according to this example are described in detail.
[0119] (step 1)
[0120]First, quartz glass as the substrate 101 was sufficiently cleaned, and a Pt film with a thickness of 200 nm as the cathode electrode 102 was formed on the substrate 101 by the sputtering method.
[0121] (step 2)
[0122] A carbon film is formed on the cathode electrode 102 by using a filament CVD (filament CVD) method. Thereafter, by implanting 1 atm% Co into the diamond-like carbon film by an ion implantation method, an electron emission film was formed. The film thickness was about 30 nm.
[0123] (step 3)
[0124] The surface termination treatment was performed under the following conditions to form the hydrogen terminated surface 104 .
[0125] Process gas: C 2 h 4 30 sccm
[0126] h 2 20 sccm
[0127] Pressure: 0.25Pa
[0128] ECR plasma power: 300W
[0129] Grid bias:...
PUM
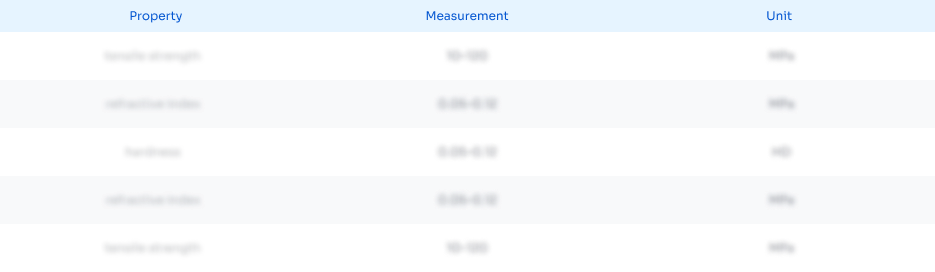
Abstract
Description
Claims
Application Information

- R&D Engineer
- R&D Manager
- IP Professional
- Industry Leading Data Capabilities
- Powerful AI technology
- Patent DNA Extraction
Browse by: Latest US Patents, China's latest patents, Technical Efficacy Thesaurus, Application Domain, Technology Topic, Popular Technical Reports.
© 2024 PatSnap. All rights reserved.Legal|Privacy policy|Modern Slavery Act Transparency Statement|Sitemap|About US| Contact US: help@patsnap.com