Assembled high molecule composite material cable stand and manufacture method thereof
A cable support and pin technology, used in pipeline supports, mechanical equipment, pipes/pipe joints/fittings, etc., can solve problems such as deformation, hidden dangers, safety accidents, etc., and achieve high surface finish, enhanced corrosion resistance, and uniform quality. good effect
- Summary
- Abstract
- Description
- Claims
- Application Information
AI Technical Summary
Problems solved by technology
Method used
Image
Examples
Embodiment 1
[0028] see figure 1 , the cable bracket of this embodiment is mainly composed of a column 101 and at least one bracket arm 102, the bracket arm 102 is connected to the side of the column 101, and the column 101 and the bracket arm 102 are respectively made of a sheet molding material mixed with steel powder become.
[0029] Among them, sheet molding compound (Sheet Molding Compound, SMC) is a type of sheet molding compound made of resin paste impregnated with fiber or chopped fiber mat, covered with polyethylene film on both sides, and then formed by pressing, so it has durability Corrosion, creep resistance, low cost, long service life and so on.
[0030] In this embodiment, the center of the column 101 has a groove, and the support arm 102 is installed in the groove, and extends horizontally. Arm 102, so that it can support multiple layers of cables.
[0031] For the convenience of installation, the column 101 can be detachably connected with the support arm 102 , for exa...
Embodiment 2
[0037] see figure 2 As shown, the preparation method of the cable support provided in this embodiment includes:
[0038] Step 201: Stir unsaturated polyester resin, tert-butyl benzoyl peroxide, aluminum oxide hydrate, polystyrene or its copolymer, magnesium oxide, zinc stearate, and steel powder to obtain a resin paste.
[0039] Add the following materials into the reaction kettle and stir to obtain a resin paste.
[0040] Unsaturated polyester resin;
[0041] Initiator: used for activating the double bond in the cross-linking monomer (polystyrene or its copolymer) to undergo a copolymerization reaction, so that the SMC is solidified and formed in the mold cavity. In this embodiment, it is: benzoyl tert-butyl oxide);
[0042] Filler: mainly hydrated alumina;
[0043] Chemical thickening agent: make the viscosity of the unsaturated polyester resin paste increase rapidly until it meets the process requirements and is relatively stable. Magnesium oxide is selected in this em...
PUM
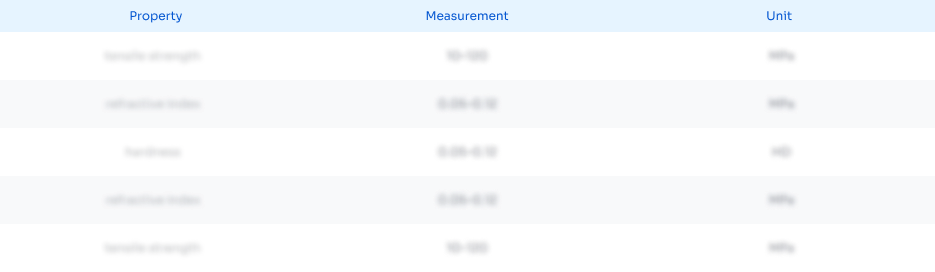
Abstract
Description
Claims
Application Information

- Generate Ideas
- Intellectual Property
- Life Sciences
- Materials
- Tech Scout
- Unparalleled Data Quality
- Higher Quality Content
- 60% Fewer Hallucinations
Browse by: Latest US Patents, China's latest patents, Technical Efficacy Thesaurus, Application Domain, Technology Topic, Popular Technical Reports.
© 2025 PatSnap. All rights reserved.Legal|Privacy policy|Modern Slavery Act Transparency Statement|Sitemap|About US| Contact US: help@patsnap.com