Coating material applied to improve thermostability of lanthanum-cerium-terbium phosphate green emitting phosphor and method of producing the same
A technology of lanthanum cerium terbium phosphate and green phosphors, applied in luminescent materials, chemical instruments and methods, etc., can solve the problems of decreased luminous efficiency, poor thermal stability, etc., and achieve small brightness attenuation, good thermal stability, and high luminous flux. Effect
- Summary
- Abstract
- Description
- Claims
- Application Information
AI Technical Summary
Problems solved by technology
Method used
Image
Examples
Embodiment 1
[0015] Prepare 200 mL of 0.01 mol / L lanthanum chloride solution and 200 mL of diammonium hydrogen phosphate solution, heat and keep at 80 °C; mix 250 g of lanthanum cerium terbium phosphate (La 0.55 Ce 0.30 Tb 0.15 )PO 4 Pour into 200mL of pure water, keep stirring at a constant speed of 30 rpm, adjust to a suspension, heat and keep it at 80°C; add lanthanum chloride solution and diammonium hydrogen phosphate solution to the lanthanum cerium terbium phosphate solution at the same time and at the same rate to suspend After the dropwise addition, stop stirring, adjust the pH value of the suspension to 5.0 with an appropriate amount of dilute acid or weak base, let it stand, and keep it at 80°C for 2 hours; filter the suspension, dry it, and add flux Mix evenly, burn at high temperature in a weak reducing atmosphere, the temperature is 1100°C, and the time is 3h; cool to room temperature in a reducing atmosphere, crush the sintered material to the required particle size, wash 4...
Embodiment 2
[0017] Prepare 200 mL of 0.02 mol / L lanthanum chloride solution and 200 mL of diammonium hydrogen phosphate solution, heat and keep at 80 °C; mix 250 g of lanthanum cerium terbium phosphate (La 0.55 Ce 0.30 Tb 0.15 )PO 4 Pour into 200mL of pure water, keep stirring at a constant speed of 30 rpm, adjust to a suspension, heat and keep it at 80°C; add lanthanum chloride solution and diammonium hydrogen phosphate solution to the lanthanum cerium terbium phosphate solution at the same time and at the same rate to suspend After the dropwise addition, stop stirring, adjust the pH value of the suspension to 5.0 with an appropriate amount of dilute acid or weak base, let it stand, and keep it at 80°C for 2 hours; filter the suspension, dry it, and add flux Mix evenly, burn at high temperature in a weakly reducing atmosphere, the temperature is 1100°C, and the time is 3h; cool to room temperature in a reducing atmosphere, crush the sintered material to the required particle size, wash...
Embodiment 3
[0019] Prepare 200 mL of 0.01 mol / L lanthanum chloride solution and 200 mL of diammonium hydrogen phosphate solution, heat and keep at 80 °C; mix 250 g of lanthanum cerium terbium phosphate (La 0.62 Ce 0.23 Tb 0.15 )PO 4 Pour into 200mL of pure water, keep stirring at a constant speed of 30 rpm, adjust to a suspension, heat and keep it at 80°C; add lanthanum chloride solution and diammonium hydrogen phosphate solution to the lanthanum cerium terbium phosphate solution at the same time and at the same rate to suspend After the dropwise addition, stop stirring, adjust the pH value of the suspension to 5.0 with an appropriate amount of dilute acid or weak base, let it stand, and keep it at 80°C for 2 hours; filter the suspension, dry it, and add flux Mix evenly, burn at high temperature in a weak reducing atmosphere, the temperature is 1100°C, and the time is 3h; cool to room temperature in a reducing atmosphere, crush the sintered material to the required particle size, wash 4...
PUM
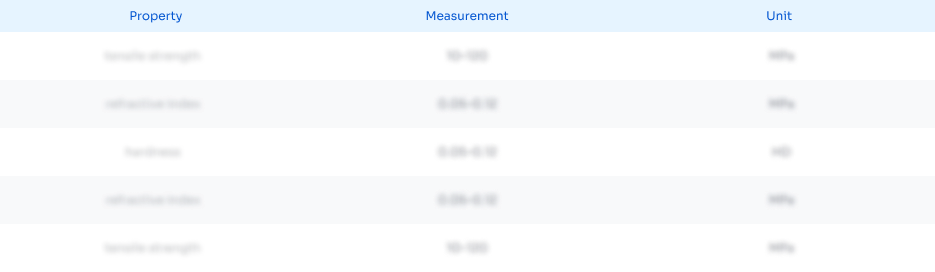
Abstract
Description
Claims
Application Information

- R&D
- Intellectual Property
- Life Sciences
- Materials
- Tech Scout
- Unparalleled Data Quality
- Higher Quality Content
- 60% Fewer Hallucinations
Browse by: Latest US Patents, China's latest patents, Technical Efficacy Thesaurus, Application Domain, Technology Topic, Popular Technical Reports.
© 2025 PatSnap. All rights reserved.Legal|Privacy policy|Modern Slavery Act Transparency Statement|Sitemap|About US| Contact US: help@patsnap.com