Process for producing flame-proof fluid sealant for construction
A technology of sealants and flame retardants, applied in the field of sealants, can solve the problems of free isocyanate damage to the environment, building sealant flame retardancy, etc., and achieve the effects of good UV stability, good adhesion, and good bonding strength
- Summary
- Abstract
- Description
- Claims
- Application Information
AI Technical Summary
Problems solved by technology
Method used
Image
Examples
preparation example Construction
[0031] The preparation method of the flame-retardant building sealant that the present invention proposes comprises the following steps:
[0032] (1) Mix the first polyol and the second polyol with each other, dry at a low vacuum of less than 2 kPa at 110°C to 140°C for 2 to 3 hours, and lower the temperature to 60°C to 70°C. The mixing mass ratio of polyols is: the first polyol: the second polyol=1:0.2~2, and then add 3~15% of isocyanates accounting for the above mixture mass percentage and 0.01~0.001% of the above mixture mass percentage Dibutyltin dilaurate, reacted for 2 to 5 hours to obtain a polyurethane prepolymer;
[0033] (2) Add a blocked silane coupling agent accounting for 3 to 15% by mass of the above polyurethane prepolymer to the polyurethane prepolymer prepared above, and react at 70°C to 80°C for 1 to 2 hours to obtain a silane blocked coupling agent. terminal polyurethane prepolymer;
[0034] (3) Stir and mix the silane-terminated polyurethane prepolymer pr...
Embodiment 1
[0050] (1) Mix 50g of polyoxypropylene diol with a molecular weight of 4000 and 15g of polyoxypropylene triol with a molecular weight of 3000, dry at 120°C for 2 hours under low vacuum, cool down to about 65°C, and add 20g of isophorone Diisocyanate and dibutyltin dilaurate accounting for 0.003% by weight of the mixture are reacted for 2 to 5 hours, and after the isocyanate radical reaches a theoretical value, the reaction is stopped to obtain a polyurethane prepolymer. Add 15 g of 3-mercaptopropyltrimethoxysilane to the above polyurethane prepolymer, and react for 2 hours under the condition of 70° C. to 80° C. to obtain a silane-terminated polyurethane prepolymer.
[0051] (2) 100 g of the above-mentioned prepared silane-terminated polyurethane prepolymer and dried 60 g nano-calcium carbonate, 0.5 g Irganox 1010, 0.4 g Tinuvin 531, 15 g dibutyl phthalate (DBP), 2 g hydrogenated castor oil, 3g of titanium dioxide and 5g of antimony trioxide were added to the planetary agitato...
Embodiment 2
[0053] (1) 60 g of polyoxypropylene diol with a molecular weight of 6000 and 15 g of polyoxypropylene triol with a molecular weight of 6000 are mixed with each other, dried under a low vacuum at 120°C for 2 hours, cooled to about 65°C, and 20g of bis-(4 -Isocyanatocyclohexyl)methane and dibutyltin dilaurate accounting for 0.003% by mass of the above mixture were reacted for 4 hours, and after the isocyanate group reached the theoretical value, the reaction was stopped to obtain a polyurethane prepolymer. Add 15 g of N-cyclohexyl-3-aminopropylmethyldimethoxysilane to the above polyurethane prepolymer and react at 70° C. to 80° C. for 2 hours to obtain a silane-terminated polyurethane prepolymer.
[0054] (2) 100 g of the above-mentioned prepared silane-terminated polyurethane prepolymer and dried 80 g nano-calcium carbonate, 0.5 g Irganox 1076, 0.4 g Tinuvin 327, 20 g dioctyl phthalate (DOP), 3 g hydrogenated castor oil, 2g of carbon black and 10g of sodium antimonate were adde...
PUM
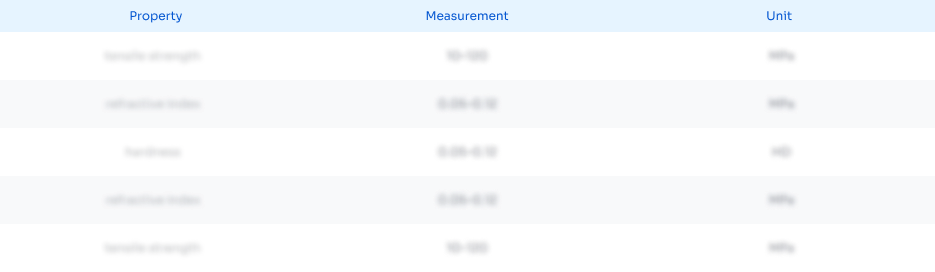
Abstract
Description
Claims
Application Information

- Generate Ideas
- Intellectual Property
- Life Sciences
- Materials
- Tech Scout
- Unparalleled Data Quality
- Higher Quality Content
- 60% Fewer Hallucinations
Browse by: Latest US Patents, China's latest patents, Technical Efficacy Thesaurus, Application Domain, Technology Topic, Popular Technical Reports.
© 2025 PatSnap. All rights reserved.Legal|Privacy policy|Modern Slavery Act Transparency Statement|Sitemap|About US| Contact US: help@patsnap.com