Process for producing vanadium oxide for implementing wastewater circulation with ionic exchange
A production method and ion exchange technology, which is applied in the field of vanadium oxide extraction, can solve the problems of high cost, low recovery rate of vanadium, and non-existence, so as to avoid environmental pollution and improve the leaching rate
- Summary
- Abstract
- Description
- Claims
- Application Information
AI Technical Summary
Problems solved by technology
Method used
Image
Examples
Embodiment 1
[0041] Using the clinker prepared in the following step (1), adopt the method of the present invention to carry out 51 rounds of waste water circulation test, from step (2) to step (6) is a round of circulation.
[0042] (1) Prepare roasted clinker:
[0043] The common vanadium slag of composition shown in table 1 is ground to below 0.098mm, gets 28kg of ground vanadium slag powder, after mixing with lime 1.96kg (ground to below 0.1mm) of CaO content ≥ 98%, after Roast at 860°C for 240 minutes in an oxidative atmosphere, take it out and cool it, and grind it to below 0.18mm for later use.
[0044] Table 1 Main components of vanadium slag (%)
[0045] V 2 o 5
CaO
MnO
P
K+Na
16.67
3.54
9.14
0.04
0.21
[0046] (2) Clinker leaching:
[0047] Take 500g of finely ground clinker, add 2000mL of the last residue washing water (clean water for the first round) to make a slurry, and continuously and slowly add sulf...
Embodiment 2
[0069] Using the clinker prepared in the following step (1), adopt the method of the present invention to carry out 51 rounds of waste water circulation test, from step (2) to step (6) is a round of circulation.
[0070] (1) Prepare roasted clinker:
[0071] Grind the vanadium slag shown in Table 5 to below 0.098mm.
[0072] Table 5 Main components of vanadium slag (%)
[0073] V 2 o 5
CaO
mn
P
K+Na
13.75
4.93
6.56
0.049
0.19
[0074] Take 28kg of finely ground vanadium slag powder, and another 1.82kg of lime (98% CaO content, ground to below 0.1mm), mix evenly with the finely ground vanadium slag, roast at 950°C for 60min in an oxidizing atmosphere, and take out After cooling, grind to below 0.18mm for later use.
[0075] (2) Clinker leaching:
[0076] Take 500g of finely ground clinker, add 1250mL of last residue washing water (clean water for the first round) to prepare a slurry, add 32wt% to 65wt% s...
Embodiment 3
[0098] Using the clinker prepared in the following step (1), adopt the method of the present invention to carry out 51 rounds of waste water circulation test, from step (2) to step (6) is a round of circulation.
[0099] (1) Prepare roasted clinker:
[0100] Grind 110 kg of vanadium slag of the composition shown in Table 9 to below 0.098 mm, and take another 7.7 kg of lime (CaO content 98%) that is ground to below 0.1 mm. Roast for 150 minutes in an oxidative atmosphere, cool the roasted clinker and grind it to below 0.18mm for later use.
[0101] Table 9 main components of vanadium slag (%)
[0102] V 2 o 5
CaO
mn
P
K+Na
12.68
2.15
5.98
0.147
0.18
[0103] (2) Clinker leaching:
[0104] Take 500g of finely ground clinker, add 1000mL of the last residue washing water (clean water for the first round) to prepare a slurry, and continuously and slowly add 32wt% to 75wt% of sulfuric acid under stirring condi...
PUM
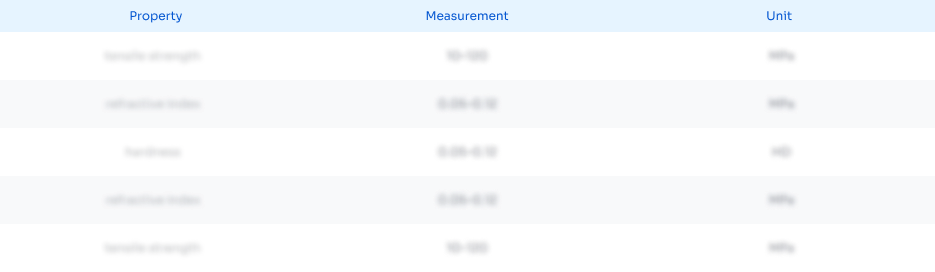
Abstract
Description
Claims
Application Information

- Generate Ideas
- Intellectual Property
- Life Sciences
- Materials
- Tech Scout
- Unparalleled Data Quality
- Higher Quality Content
- 60% Fewer Hallucinations
Browse by: Latest US Patents, China's latest patents, Technical Efficacy Thesaurus, Application Domain, Technology Topic, Popular Technical Reports.
© 2025 PatSnap. All rights reserved.Legal|Privacy policy|Modern Slavery Act Transparency Statement|Sitemap|About US| Contact US: help@patsnap.com